Armor plated steel has a history that goes back to the times of the 18-ton ‘land-ship’ or tank built in 1915 during World War I. At the time, the world’s first practical tank, ‘Little Willie’, was constructed from 0.39 inch boiler plate [1] and not much thought was given to protect it against anything other than small arms fire.
The armor plate was produced to a much higher degree of technical superiority during World War II, because of the greater ballistic challenges of the time. Frontal armor development was one field that rose quickly during the 1940s. Armor thickness advanced rapidly so as to meet the challenge of large-caliber, solid steel projectiles. WW2 also saw the launch of the Churchill Mk7, the first fusion-welded tank, and this made use of some of the first rolled homogenous armor (RHA) steel.
One of the most standard rolled or wrought armor steel grades in recent use is MIL-DTL- 12560K Class 1 RHA with hardness ranging from 250 to 410 HB (Specification, 2013) and DEF STAN 95-24 class 2–5 (specification 2002) with hardness ranging between 262 and 655. These specifications have their roots in World War II and have not changed considerably [2], although they have modified to incorporate a new class of wrought armor plate, which is heat-treatable to higher hardness ranges than DEF STAN 95-24 class 2 and Class 1 MIL-DTL- 12560K, in addition to some other minor improvements [1, 2].
Ultra-high toughness armor plate conforms to the modified MIL-DTL-12560K class 4 specification and the DEF STAN 95-24 class 4 and 5 specifications.
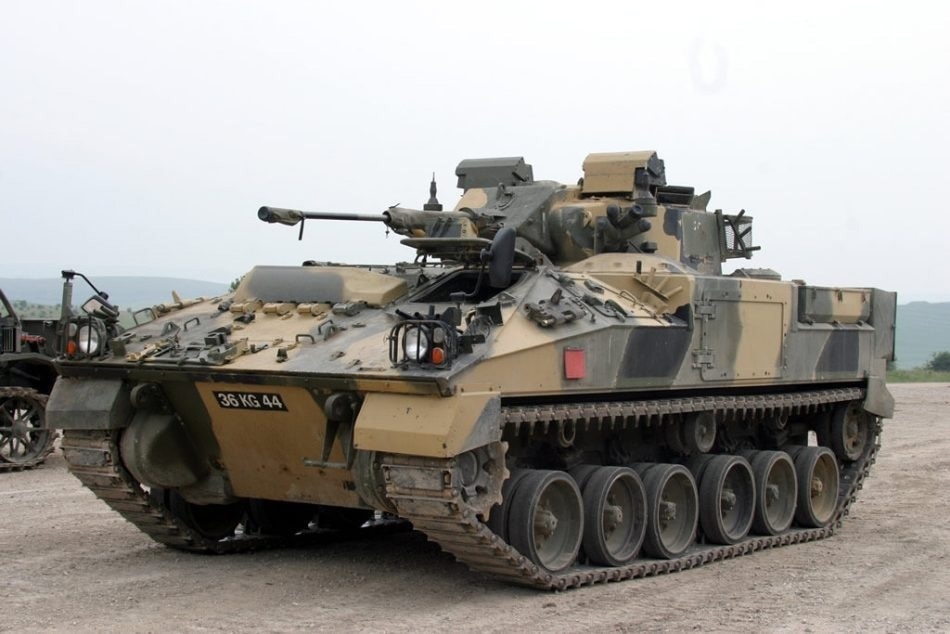
Rolled Homogenous Armor Steel (RHA)
Although armor plate has become increasingly sophisticated such that they include ceramics, multilayer composite materials, and other ballistic technologies, the model structure of an armored fighting vehicle is made from monolithic, armor-grade steel, which can last, without any metallurgical problems, for approximately three decades or more. Structural armor steels such as MIL-DTL-12560K Class 1 – 4 are selected and developed to function within harsh environments and are usually medium-carbon grades of superior- quality, realistic hardenability, and are often represented by the Cr-Mo, Mn-Mo, or Ni-Cr- Mo-(V) low-alloy steels [3].
Generally, RHA grades are low-alloy, quenched and tempered, martensitic steels, which are based upon a carbon content of 0.25% with add-ons of Cr, Ni, Mo and/or Mn for better hardenability and grain structure.
The additional requirement for this structural steel to be weldable hampers the entire alloy content to a carbon equivalent (CE) of less than 1, usually about 0.8. Most hull constructions are welded fabrications of RHA plate. It should be remembered that boosting the hardness of armor steels will usually reduce their toughness. Hardness limits are hence fixed for specific steel armor classes to control toughness during production and reduce the risk of shattering or brittle failures for specific steel compositions and applications.
MIL-DTL-12560K comes in various hardness and thickness ranges, for instance, MIL-DTL- 12560K: Class 1, 6.35 to 150.8 mm, 340 – 390 and MIL-DTL-12560K: Class 4, 420 – 470. While ballistic performance typically increases with hardness, this depends on the threat projectile and the toughness and thickness of the armor. The perfect armor choice will depend on whether the armor is to be used as appliqué armor or a stand-alone structure. The Armor Designers are required to validate whether they have selected the armor class that provides the ideal combination of structural properties and ballistic performance appropriate for the application and environment.
Armor for Modern Warfare
In real-world terms, armor characteristics such as strength/hardness/toughness are selected to deliver improved performance against a range of dangers in the battlefield, including armor piercing and fragmentation devices. It is important that such protection is provided at realistic densities for a reasonable price. Rolled armor steel such as MIL-DTL 1260K or DEF STAN 95-24 has continued to be the key armor material for various ballistic applications [4].
The ballistic performance of armor steel is a complex relationship which includes fragmentation and hardness of the steel. In investigations [5] using armor piercing (AP) and fragment simulating projectiles (FSPs), projectile shatter was revealed to be the regulating mechanism of armor performance. Against softer FSPs (281 HB), where projectile shatter is irrelevant, it was discovered that the armor performance primarily decreases with increasing plate hardness up to 450 HB due to increased susceptibility to adiabatic shear plugging. Exceeding 450 HB, the performance was seen to plateau. This performance plateau appears to relate to a significant threshold for adiabatic shear failure beyond which additional increases in plate hardness will not cause a decrease in performance [1, 6].
Masteel’s MIL-DTL-12560K and DEF STAN 95-24 Specification Armor Steel Plates
Masteel UK Ltd offers its own designation of armor steel plate (Protection 400 Armor Steel Plate) that conforms to the MIL-DTL-12560K specification in a wide range of thicknesses from 6.0 mm to 150 mm and hardness grades 250-470, and with a Brinell Hardness of 400, is perfectly suited for civilian and military based armored vehicles, in addition to security vaults and doors. Masteel’s protection 400 armor plated steel is produced through a direct quench process for good dimensional accuracy, hardness, and strength.
Evidently developed for resistance to high explosive and artillery projectiles, the steel has excellent strength and hardness, which offer incredible anti-ballistic properties. The tensile strength and yield strength of the material are 1250 MPa and 1000 MPa, respectively, offering high-grade protection against deformation and breakage.
Masteel also manufactures Protection 400 armor steel plate in accordance with the UK Ministry of Defense DEF STAN 95-24 class 2 specification. While this armor steel is technically similar to MIL-DTL-12560K class 1, it has a few small differences in the relationship between armor plate hardness and thickness. UK DEF STAN 95-24 class 2 is from a Ministry of Defense standard revised in 2002 for RHA armor plated steels used in vehicle armor applications in the UK [8].
This UK class 2 specification thickness ranges from 3 to 160 mm and the hardness ranges from 255 to 341. These figures are to some extent different from MIL-DTL-12560K class 1 which ranges from 6 to 150 mm thickness with hardness ranging from 250 to 470. Both of these specifications for armor plate are projected for use in applications where exceptional resistance to penetration is incorporated with superior structural properties. These RHAs can be cold-worked and is also amenable to welding.
Conclusion
Armored steel is anticipated to be hard and resistant to shock to guard against high- velocity metal projectiles. Steel with these features is manufactured by hot rolling cast steel billets of suitable size and then into plates of the required thickness. The grain structure of the steel (a good balance between Austenitic and Martensitic) is homogenized by hot rolling, eliminating any deficiencies which would bring down the integrity and steel strength. Moreover, rolling expands the grain structure in the steel to disperse stress loaded onto the steel across the metal, preventing stress concentration in one area.
RHA is known as homogeneous armor because its structure and composition is uniform throughout its thickness [7, 8]. In contrast, homogeneous steel plate can be case-hardened to improve its mechanical properties. The face of the steel, which starts as RHA plate, can be hardened using a heat-treatment process [6] to provide different ballistic necessities.
References
1. I Crouch, The Science of Armor Materials, Woodhead Publishing in Materials, 2017
2. Gooch, W.A., Showalter, D.D., Burkins, M.S., Thorn, V., Cimpoeru, S.J., Barnett, R., 2007. Ballistic testing of Australian Bisalloy steel for armor applications. In: Paper Presented at the 23rd International Symposium on Ballistics, Tarragona, Spain
3. Doig, A., 1979. Comparative anisotropy of quenched and tempered alloy steel plates made by high quality air melting, ESR, VIM &VAR, and VIM &ESR processes. In: Paper Presented at the Sixth International Vacuum Metallurgy Conference on Special Melting, San Diego, CA.
4. Ryana,.H.Lib.et al,. The ballistic performance of an ultra-high hardness armor steel: An experimental investigation, International Journal of Impact Engineering, Volume 94, August 2016, Pages 60-73,
5. L. Woodward, The Penetration of Metal Targets by Conical Projectiles, Int. J. Mech.Sci., Vol. 20, 1978, pp. 349-359.
6. Tabor, The Hardness of Metals, Clarendon Press, Oxford, 1951, p. 108.
7. MIL-DTL-12560K (MR), 7 December 2013
8. Ministry of Defence, Defence Standard 95-24, Issue 2 Publication Date 2 September 2002, Armour Plate, Steel (3-160 mm)
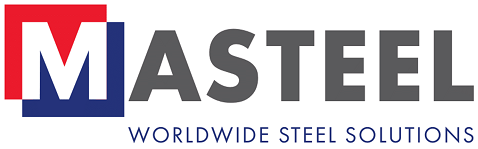
This information has been sourced, reviewed and adapted from materials provided by Masteel UK Ltd.
For more information on this source, please visit Masteel UK Ltd.