In many cases, selecting the most appropriate mounting material for a sample is straightforward. For example, Bakelite or epoxy are suitable choices when a uniformly-shaped mount is needed to hold a sample.
In circumstances where a mounting material must permit the analyst to observe the sample mounted within, however, Lucite is the ideal choice.
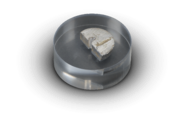
Image Credit: LECO Corporation
Lucite is an acrylic thermoplastic that initially exists as loose granules. These granules are cured into a transparent solid that exhibits good hardness and edge retention.
The most significant advantage of Lucite lies in the analyst’s ability to see all sides of the sample. This is beneficial when visually identifying the sample when ascertaining the optimal depth to grind and polish to.
Lucite can be challenging to implement as a mounting material because it requires precisely managed temperature and pressure to obtain clear results.
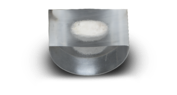
Image Credit: LECO Corporation
If a Lucite mount fails to cure at the correct temperature, the materials inside will remain porous and uncured. This leads to the presence of a ‘cloudy’ or ‘cotton ball’ effect that reduces visibility through the material and may impact the grinding and polishing process.
Should the center be too cool, granules at the mount’s core will not melt, and the cloud will appear blurry.
Should the center be too hot as the mount’s exterior hardens, this will contract as it cools and leave a grainy cloud that may lead to bulging or cracking in the mount. These flaws diminish the utility of Lucite in either scenario.
One conventional Lucite mounting method involves over-heating the exterior of the mount to 150 °C (~300 °F) before maintaining this temperature for approximately 10 minutes. This ensures sufficient time for the center to melt before allowing it to cool at a slow rate of 0%-5%.
The mount temperature will remain uniform throughout as it hardens, but this technique is not always successful.
LECO remained unsatisfied with this traditional method, so the company began experimenting with looking for alternatives.
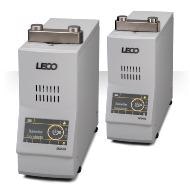
Image Credit: LECO Corporation
This experimentation aimed to produce consistently and perfectly clear Lucite mounts, with every MX400 and MX500 mounting press programmed with a reliable method suitable for application in any lab.
A more appropriate strategy was developed. This involved reducing the temperature to 105 °C (220 °F) - slightly above Lucite’s melting temperature - and maintaining this for 13+ minutes (depending on the mount size) prior to applying a quick cooling rate of 100%.
This method ensured that the mount’s center was never overheated. It also guarantees that the mount’s center reaches a hot enough temperature to melt completely.
The use of this lower temperature also meant that Lucite became a viable mounting option for temperature-sensitive samples, for example, circuit boards.
Lucite is still incredibly challenging to perfect, even with an improved method in place. Even slight changes to the samples or atmosphere can negatively impact the mounting process.
LECO’s revised method allows users to make specific tweaks to accommodate these differences. For example, where mounts exhibit a blurry cloud in the center, it is possible to increase the hold time or temperature.
In cases where mounts exhibit a grainy cloud in the center, it is possible to reduce the temperature or slow the cooling process.
Once the method has been adjusted to meet the specific needs of the samples, the MX-Series of mounting presses will be able to efficiently and reliably create mounts - a single yet vital step in LECO’s beginning-to-end metallographic solution.
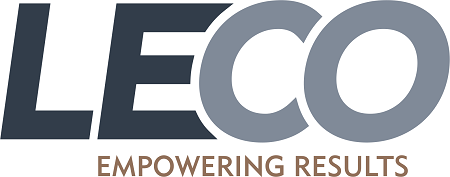
This information has been sourced, reviewed and adapted from materials provided by LECO Corporation.
For more information on this source, please visit LECO Corporation.