Compressed air is regarded as the fourth utility after water, power and fuel (natural gas), and generally the one that all customers should generate and offer themselves. Compressed air is the energy of choice for powering a wide range of applications over industrial and fleet applications. Since compressors are essential to offer the power for various machines on a vehicle or throughout a plant, uptime and reliability of compressors are highly important factors.
Oil analysis is an essential tool employed for assuring that compressors stay up and running and that unplanned downtime is reduced. This short Ask the Expert video describes the parts of a compressor that are usually monitored using oil analysis, what types of tests are normally run on the oil, the most common failure modes for compressors, and what on-site instruments are ideally suited to execute that series of tests.
Ask the Expert: Compressor Oil Analysis
Compressors are analogous to pumps since both increase the pressure on a gas or a liquid and help it progress through a mechanical system. Compressors are mechanical devices concentrated on compressing and moving gases. Air compressors usually take in a large mass of air and compress it to a smaller mass, thereby increasing the pressure enormously.
Similar to pumps, compressors are classified into positive displacement and dynamic methods, based on the principle of operation or technology. The market is classified as reciprocating, centrifugal and rotary compressors. In 2014 the rotary/screw segment accounted for above 45% of the world market, with compressed air being the main application.
Oil-free air compressors contain 30% of the compressed air market. This growth is attributable to a growing requirement for high-quality compressed air, generally for pharmaceutical or food and beverage manufacturing. The term “oil-free” merely means that the gas is not mixed with lubricant.
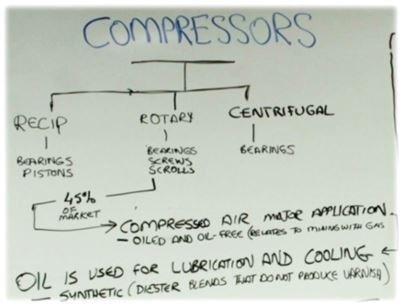
In all compressors, bearings are the component that should be lubricated and monitored. Rotary positive displacement compressors also have vanes, screws or lobes which are lubricated - normally by the fluid they are pumping, which may be an oil/air mix, or a lubricant.
One of the most significant functions of a compressor lubricant is to carry out heat removal in the air end. Since the air is compressed, it produces a large amount of heat. The gears, bearings, and seals will all fail fast if this heat is not eliminated quickly. Inadequate heat removal can be traced to the contaminated lubricant or the wrong lubricant type being employed.
Contaminated lubricant (also called coolant, on account of its importancein heat removal) can take place due to inlet air quality problems like:
- External air contamination (SOx, NOx from nearby engine exhaust)
- Particle-laden air (clogged filters)
- High moisture (saturated coalescers filters, or no air driers)
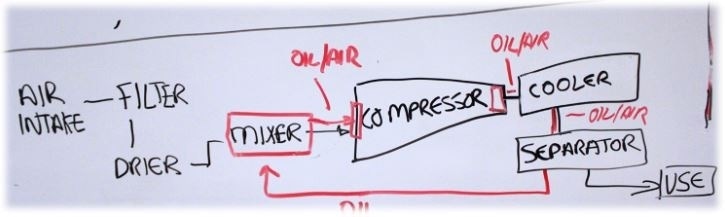
Consequently, it is sensible to monitor the oil for contamination due to airborne particles, for instance dirt and sand. It is also essential to monitor the oil for water as it can induce corrosion in the system as well as influence the acidity and viscosity of the lubricant.
Similar to any mechanical system, viscosity is a vital test to run on the compressor oil. Generally, the occurrence of some other failure mode is indicated by the changes in viscosity. Water contamination testing is crucial to assure that moisture does not enter into the system.
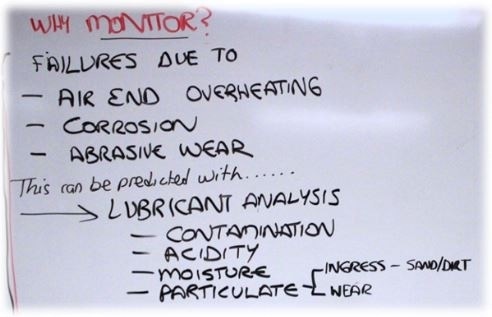
The degradation of oil due to extreme heat or acid formation from moisture is demonstrated by IR and TAN. Particulate count and categorization can determine whether there is mechanical wear taking place or whether there is external contamination entering the system because of poor air filters that might cause a failure. Elemental analysis helps in determining the source of particulates and whether the additive levels in the oil have been exhausted.
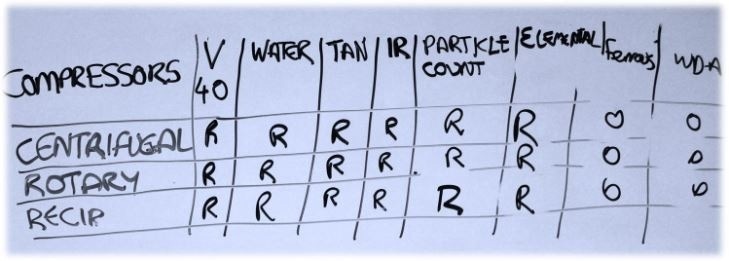
Optional tests one might want to consider for compressors include ferrography and wear debris analysis (WDA). WDA explains either an analytical or a patch method that separates magnetic wear particles from the oil and deposits them on a glass slide called a ferrogram. Microscopic investigation or the patch or slide allows characterization of the wear mode and predictable sources of wear in the machine. This method is called as analytical ferrography. It is a good indicator of abnormal non-ferrous and ferrous wear, yet it is generally only performed by skilled analysts.
The suggested tests can be easily performed on-site by the MiniLab Series of analyzers for industrial settings. The oil condition and chemistry are measured by MiniLab 23 and 33. The MiniLab 53 counts and categorizes particles, and measures ferrous wear. The MiniLab 153 includes an elemental spectrometer for analyzing the concentration of additives and wear metals.
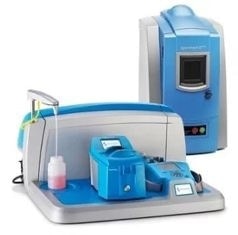
Experts suggest the MicroLab 40 oil analyzer for mobile applications such as mining, trucking and other applications using heavy transport equipment.
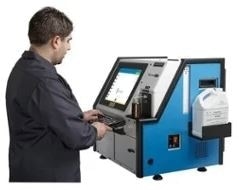

This information has been sourced, reviewed and adapted from materials provided by AMETEK Spectro Scientific.
For more information on this source, please visit AMETEK Spectro Scientific.