In a recent article published in the journal Technologies, researchers developed new techniques to enhance the safety and sustainability of mine waste management. The project focuses on using advanced technologies, such as drones and ground sensors, to monitor mine sites more effectively. The research seeks to apply electromagnetic measurement technologies to mining, already successfully used in agriculture.
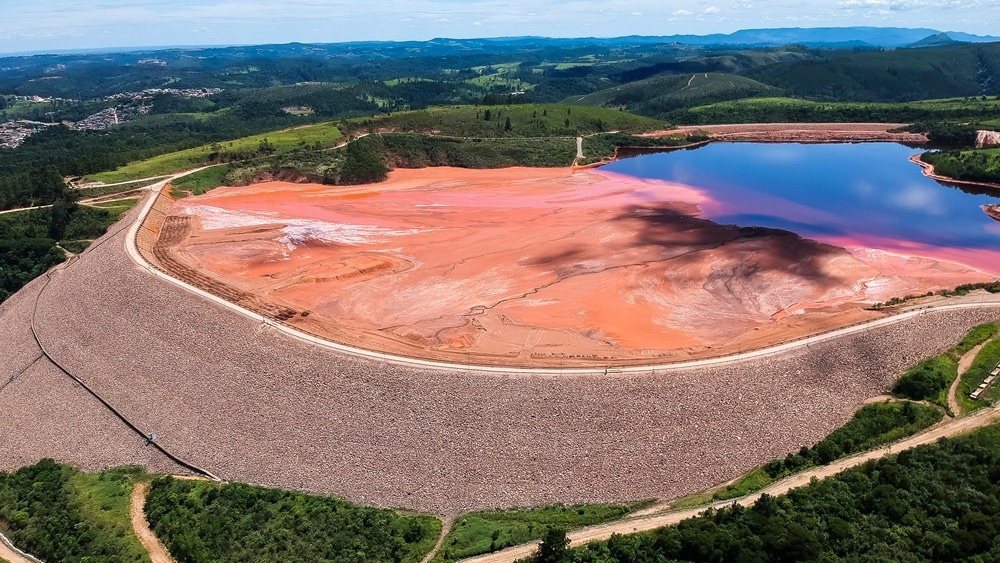
Image Credit: ArtbyPixel/Shutterstock.com
Background
Effective mine waste management is one of the most significant environmental challenges facing the mining industry today. As global demand for minerals like nickel, copper, and cobalt grows due to their use in renewable energy technologies, the volume of mining waste is expected to increase substantially.
Current monitoring techniques, such as drilling, are costly and often produce unreliable data, making it difficult to manage waste effectively and ensure the safety of mining operations. By providing more precise and cost-effective monitoring, these techniques could play a critical role in improving mine site safety, environmental protection, and land rehabilitation.
The need for these advancements is increasingly urgent as global demand for critical minerals continues to rise, contributing to more extensive mining activities and, consequently, more waste. Integrating geochemical data from mine waste with electromagnetic measurements offers the potential for more accurate, real-time monitoring of soil, water, and rock conditions at mine sites.
The Current Study
The article covers the core theoretical aspects of 3D sensing, point cloud processing, Bird’s Eye View (BEV) imaging, and the YOLO v8 algorithm. LiDAR, 3D Time-of-Flight (ToF), and stereo cameras are commonly used for 3D perception, as they effectively capture high-resolution data in complex environments.
Point clouds represent 3D spatial data as sets of points, each with coordinates (X, Y, Z) and attributes like color or segmentation ID. These unorganized point clouds pose difficulties in processing, but common techniques like downsampling, registration, and Random Sample Consensus (RANSAC) are used to manage these issues.
Point cloud registration is essential for reconstructing 3D objects from different viewpoints. The Iterative Closest Point (ICP) algorithm is often used for alignment. RANSAC, an algorithm for robust model estimation, identifies and utilizes inliers while ignoring outliers, ensuring reliable results even with noisy data.
The rock centroid localization system was designed in three stages: assembly, data acquisition, and data processing. Sensors were strategically positioned to capture maximum data from target rocks, and a Basler Blaze-101 3D ToF camera was used for its precision and durability in indoor and outdoor environments.
The camera provided high-quality images ideal for mining applications. Despite the widespread use of LiDAR in 3D sensing, its lower resolution and point density made it less suitable for detailed rock detection, especially in overlapping or stacked rock environments. In contrast, the Basler Blaze-101 camera offered superior depth maps, resolution, and texture data. The system incorporated robust features like real-time processing and camera redundancy to prevent data loss, ensuring reliable operation.
Results and Discussion
The rock centroid localization system achieved excellent results, with robust performance in various challenging mining scenarios. Using the YOLO v8x-Seg algorithm, the system's segmentation demonstrated high accuracy, achieving an Intersection over Union (IoU) of over 93% in overlapping and non-overlapping environments. Sensitivity analysis showed the system's resilience to image perturbations such as brightness and contrast changes, although performance slightly dropped with rotations. Rock centroid localization results revealed high precision, particularly in the XY plane, with minimal errors and consistent accuracy across different scenarios. While the Z-axis showed a higher error margin (up to 22%), it did not significantly impact overall performance.
Graphical analysis of rock segmentation and centroid localization validated the system's effectiveness, even under challenging conditions like overlapping and varying lighting. The system's real-time capabilities, with quick data acquisition and processing times, make it suitable for practical mining applications.
The study identified potential improvements, such as sensor fusion with thermal cameras, to address performance degradation caused by suspended particles. Overall, the system demonstrates high adaptability to different sensors and environments, underscoring its potential for autonomous rock-breaking operations in mining.
Conclusion
In conclusion, the article introduces an efficient rock centroid localization system designed for mining robotic applications, specifically rock-breaking hammers. It maintains consistent performance in various lighting conditions and with suspended particles, which are critical factors in real-world mining.
Sensitivity analysis confirmed its robustness, although it showed some vulnerability to rotational perturbations. Despite these minor limitations, the system’s processing speed of approximately 5 seconds makes it suitable for real-time applications.
Future improvements will focus on refining preprocessing techniques, enhancing input resolution adaptability, and exploring image fusion methods to handle diverse environments more effectively. Integrating new technologies, such as super-resolution techniques and multimodal data fusion, will enhance its adaptability and performance.
Source:
Kern J., Rodriguez-Guillen R., et al. (2024). Enhancing 3D Rock Localization in Mining Environments Using Bird’s-Eye View Images from the Time-of-Flight Blaze 101 Camera. Technologies 12, 162. DOI: 10.3390/technologies12090162, https://www.mdpi.com/2227-7080/12/9/162