Metal reprocessing is an important commercial activity in several industries. This article will look at metal reprocessing in mining and provide an overview of recent advancements in this field.
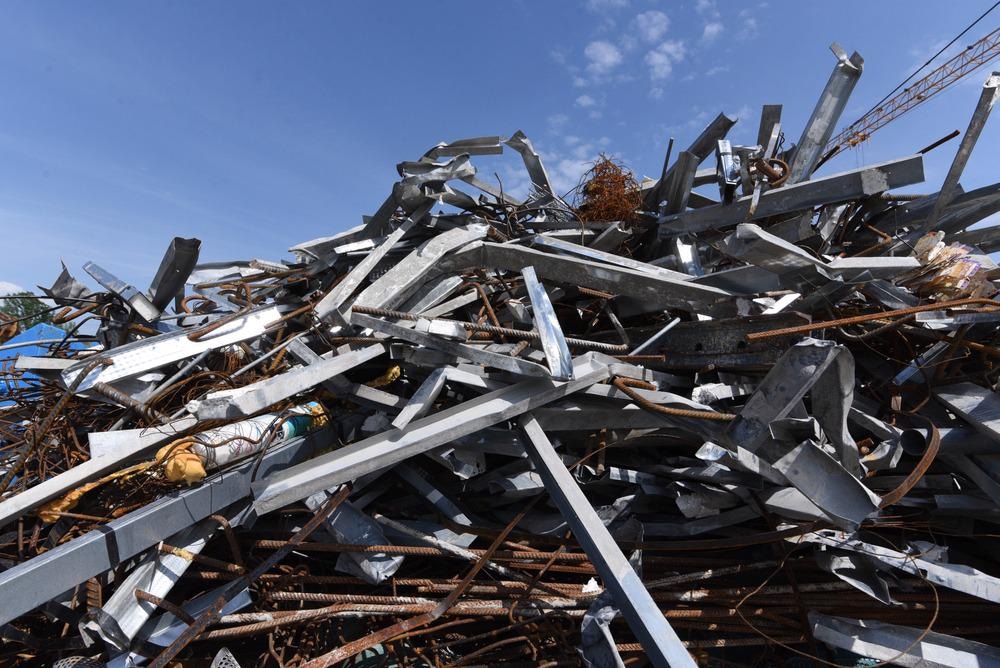
Image Credit: elmar gubisch/Shutterstock.com
What is Metal Reprocessing?
Metal reprocessing is the value-added process of recovering vital metal resources for further commercial use. One of the most common examples of metal reprocessing is the recycling of scrap and waste metal from industries such as construction, the automotive sector, and aerospace, as well as recycling domestic products such as aluminum food cans.
In reprocessing, metals are collected, sorted, processed, melted, and purified. Valorizing metals, such as all waste streams, is advantageous for the industry in the following ways:
- It reduces the environmental impact of resource extraction
- Prevents pollution, emissions and the build-up of waste products in the environment
- Overcomes dwindling natural resources issues
- Economic benefits
Metal Reprocessing in the Mining Industry
As the world moves toward a low-carbon economy, there is an increasing urgency in reusing critical resources and reducing emissions. Mining is a key economic industry that is responsible for vast quantities of waste materials.
Aside from vital resources going to waste, many of the technologies that assist the move toward a post-carbon economy rely on critical metals. There is a huge opportunity in the mining industry to improve the efficiency of resource exploitation and processing in the mining industry.
Mining waste has different properties to those possessed by virgin ores. This means that the technology required to process these resources is vastly different from the methods used to process mining ores. Liberation, separation, and concentration of these critical waste resources require entirely different processes to realize efficiently.
Millions of tons of mining tailings are produced annually, with billions of tons of valuable metal resources being contained in legacy dams. Aside from these resources being lost, their proliferation in the environment causes significant damage to vulnerable ecosystems. Recovering them provides opportunities for environmental reclamation and generating additional revenue for mining companies. Reprocessing turns tailings ponds from a liability into an asset.
Standard Tailings Reprocessing Methods
Currently, the standard method for reprocessing tailings involves physically collecting tailings from dams and dragging them back to the concentrator. Mineral processing solutions are then used to extract valuable resources. Water is removed from the discarded materials and recycled for use in mining operations. This helps reduce costs and cleans up tailings dams, helping to improve the environmental remediation of mining operations.
Processes for Extracting and Valorizing Mining Wastes
Circular mining is a concept where minerals are processed and metal is extracted, recovered, and any residues are valorized. There have been several developments in recent years that have helped to transform mining from a linear into a circular industry.
Several technologies have been explored to achieve this concept. Processing technologies need to be developed or adapted to current operations. While there are unique challenges that must be overcome in treating mine wastes compared to processing ore, the processing steps are essentially the same. The difference is the type of technologies applied in each sub-processing step.
Comminution is a multi-stage process that sequentially reduces ore particles, creating progressively finer particle sizes. Greater degrees of mineral liberation is achieved. The first stage is crushing, and once finer-sized particles are produced, grinding or milling is used.
Different grinding media are used in mills, including ore pebbles, steel balls, steel rods, ceramic media, and a mixture of pebbles and steel balls. As particle sizes in mining waste can vary, this process may not be suitable for fine particle-sized waste products.
Stirred milling is an attrition method that has advantages in terms of energy efficiency, footprint, and cost. Cylindrical vessels, either horizontal or vertical, are filled with grinding media for processing waste slurries. Coarse particles and grinding media are retained, with the feed discharged through a classifier. This method is suitable for coarse and fine-grained waste.
Classification methods are integral to processing mining waste and tailings and recovering valuable minerals and metals. Classification is important for mining wastes as it separates low-grade materials for further processing. Screens and hydroclones are two examples of commonly used classification components.
Flotation methods are used in mining tailings and processing waste recovery and reprocessing. In conventional flotation methods, air is introduced by an impeller and forms bubbles. Particles that attach to the bubbles float to the top of the tank and are collected, whereas those that do not are discharged.
Mineral processing commonly uses pneumatic and mechanical flotation cells. Flotation methods include floc flotation, fluidized bed flotation, and reactor-separator induced air flotation. Gravity separation techniques can also be employed for mining waste treatment and metal reprocessing and recovery.
The Future of Metal Reprocessing
Mining operations are becoming more circular as the importance of mining waste recovery to mitigate the effects of climate change and dwindling resources becomes clearer. A real-world example of a company that is implementing a more sustainable, circular approach to this issue is EnviroGold Global Ltd.
The Buchans Tailings and Hellyer’s Tailings reprocessing projects are predicted to reduce greenhouse gas intensity per gold ounce by 96% and an energy intensity reduction of 80% compared to industry averages. EnviroGold’s approach is heavily analytics-driven. A total of 325 global tailings sites have been analyzed by the company. It has announced that it has eight projects in the works.
Innovative approaches to waste management and recovery are central to improving the sustainability and environmental friendliness of the mining industry. Advances in metal reprocessing technologies have vast potential for achieving this aim.
References and Further Reading
Gouveia, R (2019) How to generate value from tailings with reprocessing to be future ready? [online] mogroup.com. Available at: https://www.mogroup.com/insights/blog/mining-and-metals/how-to-generate-value-from-tailings-with-reprocessing-to-be-future-ready/
Witworth, A.J (2022) Review on advances in mineral processing technologies suitable for critical metal recovery from mining and processing waste. Cleaner Engineering and Technology 7 [online] Available at: https://www.sciencedirect.com/science/article/pii/S2666790822000568
Gleeson, D (2022) EnviroGold highlights sustainable metal reprocessing credentials at Hellyer, Buchans Tailings projects [online] im-mining.com. Available at: https://im-mining.com/2022/03/09/envirogold-highlights-sustainable-metal-reprocessing-credentials-at-hellyer-buchans-tailings-projects/
Disclaimer: The views expressed here are those of the author expressed in their private capacity and do not necessarily represent the views of AZoM.com Limited T/A AZoNetwork the owner and operator of this website. This disclaimer forms part of the Terms and conditions of use of this website.