Mining technology and equipment have evolved significantly over the years, transforming exploration methods and improving efficiency in the overall mining process. From early hand tools to modern sophisticated machinery, advancements in mining equipment have greatly improved exploration accuracy, speed, and safety.1-3
This article provides an overview of mining equipment used in exploration, including its historical development and recent technological innovations shaping the industry.
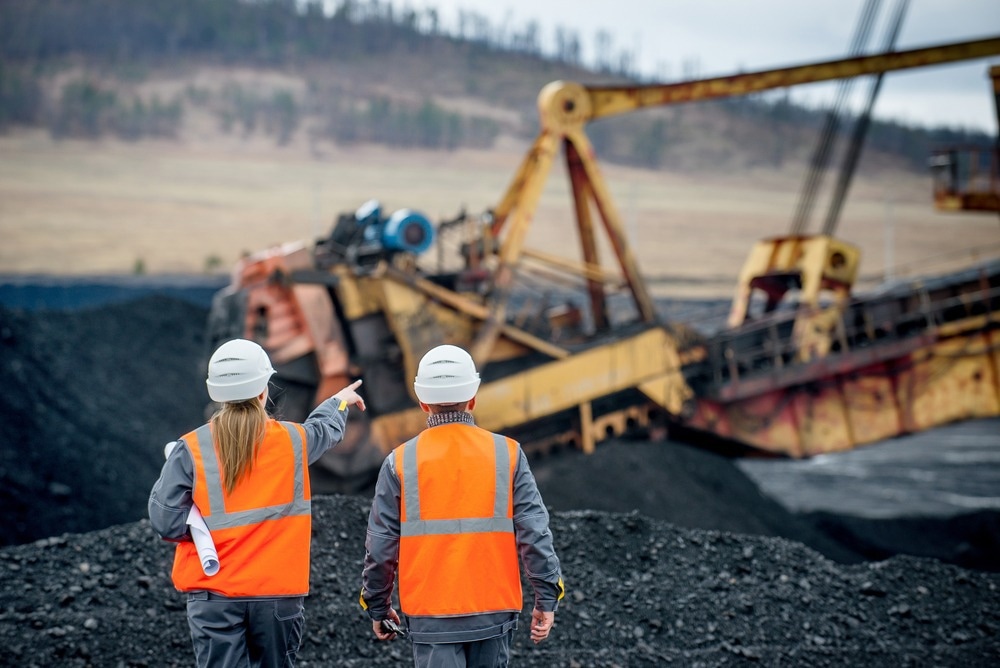
Image Credit: Mark Agnor/Shutterstock.com
History of Mining Technology
The history of mining equipment began with simple tools like hand digging and stone tools, which were slow and inefficient. The fire was later introduced, where large stacks of logs were set alight to crack rock faces and allow miners to dig deeper more quickly. However, a major leap in mining technology came with introducing explosives during the Middle Ages.1
Black powder was used to fragment rock, but the true transformation occurred in the 19th century with the invention of dynamite, revolutionizing mining. This period also saw the development of motorized mining tools like drills and steam-powered pumps. The Industrial Revolution marked the peak of mining advancements, with innovations such as compressed air drills, mine cars, and steam pumps.1
These improvements drastically enhanced mining efficiency and capacity, marking a profound shift in resource extraction. Mining operations became more productive as technology advanced, leading to larger-scale mining and greater resource accessibility.1
Overview of Mining Equipment
Mining depends on advanced technology and equipment to efficiently process and extract mineral resources, ensuring safety and minimizing environmental impact. The equipment utilized in mining operations varies based on the material type being extracted, the geographical context, and the employed mining method.
Surface and underground mining equipment are the two primary equipment categories used in mining.1,2
Surface mining equipment
Surface mining involves removing large amounts of earth to access minerals near the Earth's surface. Surface mining techniques include open-pit mining, strip mining, and mountaintop removal. It is typically used for minerals located in shallow deposits.1
This mining method uses heavy machinery designed for large-scale operations for mineral exploration. Key mining equipment includes wheel loaders, drilling machines, excavators, mining/dump trucks, and bulldozers. Excavators are large machines used in the digging and removal of overburden to access the underlying ore.1
These machines have a rotating arm and different attachments like hydraulic arms/buckets. For instance, bucket-wheel excavators used in open-pit mining continuously transport, dig, and load materials.1
Similarly, dragline excavators are one of the largest pieces of land mining equipment used to remove overburden in strip mining. In this equipment, a massive bucket system is attached to large booms and dragged across the earth's surface for excavation.1
Bulldozers are crucial for land clearing as they effectively push material and prepare the site for mining operations. They can operate in diverse terrains as their wide tracks improve stability and mobility.1
Drilling machines create holes for exploration/blasting and are available in different designs, like percussion and rotary drills, which are used based on geological conditions. Blasthole drills drill holes into the earth’s surface to place explosives.1
Dump trucks, designed to carry large volumes, are used to transport mined materials. Their dump beds allow quick unloading at processing sites. Wheel loaders are versatile machines used for transporting and loading materials. They are equipped with a front-mounted bucket that lifts/scoops heavy materials.1
Underground mining equipment
Underground mining involves digging tunnels or shafts to reach deeper mineral deposits. This method is used when minerals are located far beneath the surface. It requires careful planning and safety measures due to the risks of collapse and ventilation issues.1
Equipment used in this mining method is designed to navigate confined spaces and narrow tunnels. Key equipment includes mine cages, continuous miners, room and pillar equipment, face haulage systems, and rock drills.1
Continuous miners are critical in underground mining as they remove material while advancing, enabling continuous mineral extraction. They have a large rotating drum with carbide teeth to scrape the mineral-like coal from seams. Continuous miners also have conveyor belts for mineral transportation, making this a remotely controlled automated process.1
Room and pillar equipment create mine layouts featuring parallel entries with supportive pillars remaining intact. Shuttle cars and roof bolters are key components of this system. Mine cages transport materials and personnel to and from underground locations through vertical shafts.1
Materials from the mining face are transported to the underground processing facilities using the face haulage systems. Rock drills are used for blasting and preparing the mining site for different operations. Haulers and loaders are highly maneuverable and compact mining tools that load and haul away minerals.1
Advances in Mining Technology and Equipment
Mining technology and equipment advances have significantly enhanced the operational safety, efficiency, and sustainability of resource extraction.
Automation
In mining, automation involves using artificial intelligence (AI) and robotics to optimize operations. Automated trucks transport materials without human intervention, improving site safety and reducing labor expenses.1,3
Fully autonomous mining trucks using radar and light detection and ranging (LiDAR) technology can freely navigate a mining site. Similarly, robotic drilling systems operate in hazardous environments, which minimizes the risk to human labor.
Artificial intelligence (AI) has been used in blasting to optimize blast designs with blast and parameters, leading to reduced vibrations and improved fragmentation.1,3
Drone technology
Drones are increasingly used for monitoring, mapping, and surveying purposes. Offering an aerial perspective of mining sites allows for more accurate safety inspections, environmental assessments, and resource estimations. These machines improve data collection efficiency significantly, enabling real-time decision-making and analysis.
In underground mining, drones are used to visually inspect ore passes, stopes, conveyor belts, and ventilation shafts. They enable inspections in potentially risky zones of underground mines.1
Geochemical and geophysical tools
Modern mining depends on advanced geophysical methods like resistivity surveys and seismic reflection to find mineral deposits. These technologies provide data critical to determining the exploration strategy, reducing the risk and uncertainty with mining ventures. Geochemical analysis assesses the ore quality and determines the process viability.1
Real-time monitoring systems
These systems use the Internet of Things (IoT) technology and sensors to track environmental conditions and equipment performance. They provide important data that enhances safety protocols and maintenance scheduling, and streamlines operations.1,3
New Developments in Mining Technology and Equipment
A work recently published in Expert Systems with Applications explored the challenges of implementing green and climate-smart mining and developed a decision support system to address these obstacles. A case study of the Chinese mining industry revealed critical challenges related to government, regulatory, technical, and operational categories. The study proposed three strategies to overcome these challenges, including low-interest loans, cognitive development, and stricter regulations for new enterprises. This research contributes novel insights to integrate mining practices with sustainability science.4
Conclusion and Future Outlook of the Mining Industry
Mining technology and equipment have evolved substantially from simple hand tools to advanced automation and robotics, improving efficiency and safety. With innovations in automation, drone technology, and real-time monitoring, the industry is poised for further transformation.
Future advancements are expected to focus on reducing mining's ecological impact while optimizing resource extraction. Eventually, the integration of cutting-edge technologies will shape a more sustainable and efficient mining industry.
Continue Reading: The Main Types of Mining and their Differences
References and Further Reading
Bozdemir, B. S. (2024). Introduction to Mining Engineering-Comprehensive Volume-1. https://books.google.co.in/books?hl=en&lr=&id=aJsjEQAAQBAJ&oi=fnd&pg=PA100&ots=Os2r0sIkSV&sig=FKrJ0qlNRqW_54gRpGBUcmk2ciQ&redir_esc=y
An Introduction To Mining [Online] Available at https://www.sgu.se/en/itp308/knowledge-platform/2-intro-mining/
Long, M., Schafrik, S., Kolapo, P., Agioutantis, Z., Sottile, J. (2024). Equipment and Operations Automation in Mining: A Review. Machines, 12(10), 713. DOI: 10.3390/machines12100713, https://www.mdpi.com/2075-1702/12/10/713
Jiskani, I. M., Cai, Q., Zhou, W., Lu, X., & Shah, S. A. A. (2022). An integrated fuzzy decision support system for analyzing challenges and pathways to promote green and climate-smart mining. Expert Systems With Applications, 188, 116062. DOI: 10.1016/j.eswa.2021.116062, https://www.sciencedirect.com/science/article/abs/pii/S0957417421014020
Disclaimer: The views expressed here are those of the author expressed in their private capacity and do not necessarily represent the views of AZoM.com Limited T/A AZoNetwork the owner and operator of this website. This disclaimer forms part of the Terms and conditions of use of this website.