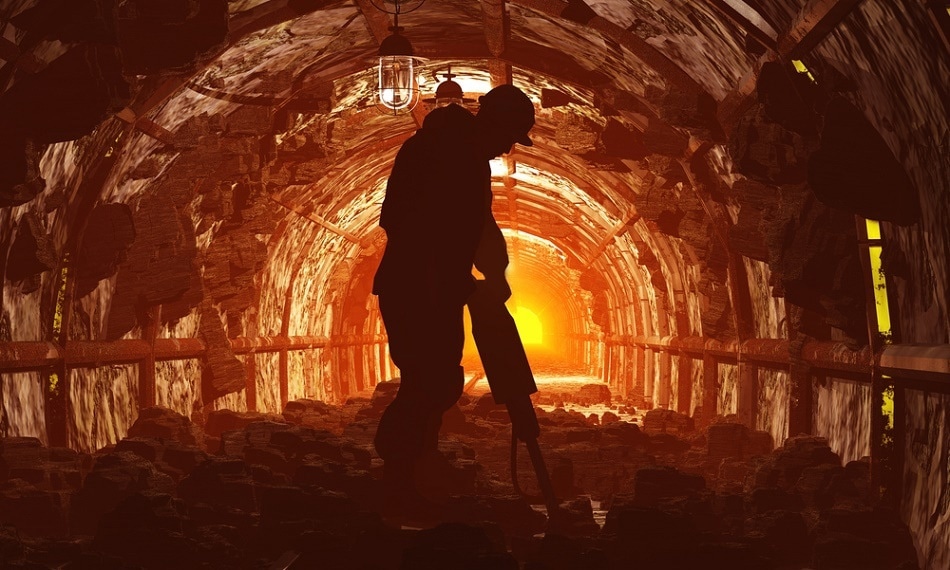
iruii/Shutterstock.com
Many of today's mining operations are in remote locations and these operations pose particular issues for both equipment and workers. Mistakes and fatigue can both lead to injuries, while staffing shortages, bad weather, and insufficient infrastructure pose further challenges.
Automation is one way that mining companies can optimize their operations. Equipment automation handles many issues in today’s competitive mining industry. Automation also boosts the degree of predictability in mining operations, an attractive aspect for financial and budgetary reasons.
Some industry analysts have warned that automation isn’t a one-size-fits-all solution, with new mining operations, growing sites and very remote mines being the best candidates for the technology. Mine locations that have been around for decades should meticulously assess the business case to make use of automated technologies to determine if, when, and where they best boost productivity, increase safety, and lower costs.
Automation Applications
A mining operation is a combination of multiple activities, from drilling, blasting and carrying material right through to smashing and milling, as well as refining and transportation of the product. The automated control used in many drilling operations, allows an operator to configure and run the equipment remotely. This removes the operator from potentially hazardous areas on the drill rig or in the area being mined and boosts the overall efficiency of the operation.
Swedish company Sandvik Mining offers a range of automated equipment for use throughout the mining industry. Its products allow operators to control equipment remotely to improve time management and efficiency of operations. For example, the AutoMine Hauling solution allows a sole operator to remotely control a number of trucks and operations from a single control room, ensuring optimal production planning and safety.
Remote automation relies highly on the use of sensors that are capable of offering the information needed to manage mining and processing operations. Advances in information processing allow these sensors to evaluate signals and incorporate data from several sensors. AI software then allows computers to use sensor information in ways that allow machinery parameters to be changed throughout the mining operation.
New sensing technologies such as GPS, radar, and laser systems being incorporated into robotics will have an increasing impact on the safety, predictability, precision and efficiency of mining.
Robotics advancements are altering mining all around the planet. Completely automated robotic mining uses smart drills for both extraction and material recognition. Automated mining operations also use automated vehicles for the remote-controlled movement of materials.
Artificial intelligence systems using GPS systems, wireless connectivity and sensors, enable driverless trucks to either drive on their own or be driven by a remote operator. Computer systems that supply data on the velocity and position of the vehicle can stop accidents and improve the lifetime of these machines. Productivity loss can be reduced as breakdown regularity diminishes resulting in enhanced productivity and profitability.
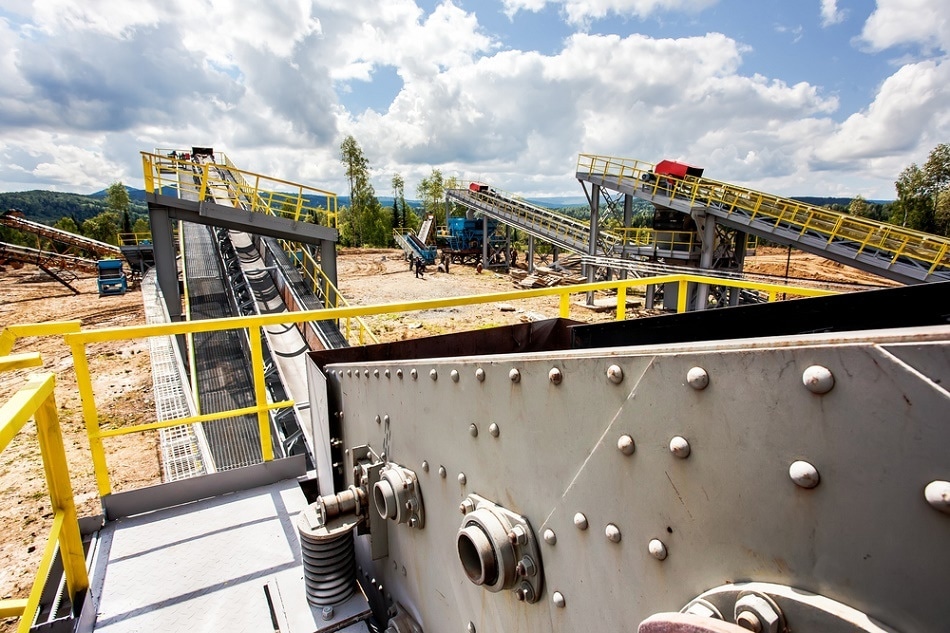
Yermolov/Shutterstock.com
Automation boosts energy productivity by lowering variation and escalating uniformity in the operation of equipment. Through the use of intelligent sensor technologies, situational awareness can boost the productivity and sustainability of the mining operation. The steadier operation of equipment has also been shown to lower emissions. Lots of other advantages stem from this efficiency, including decreased fuel use and operating costs.
ASI Mining focuses on increasing safety during mining processes. Their line of remotely controlled excavators ensures safety for an operator as any unstable terrain, falling debris or any other hazard can be avoided. By removing the operator from any potential dangers, automation of equipment can improve safety standards across all areas of mining, and narrow the margins for error during operations.
The use of robotics allows more selective and precise mining. Ecological tracking systems and devices with wireless communications can precisely monitor and evaluate variables like ground water amounts, subterranean ventilation and temperature shifts. These tracking systems enable businesses to observe and record the ecological effect of their mining activities, which can lead to eco-friendly operational adjustments.
Intelligent devices also enable the control of machinery to maximize and lower energy and water usage, precious resources for the mining industry. Automated alerts notify management to minimize the impact of environment-damaging accidents and supports energy-efficient practices.
The Future of Mining Automation
Advances in AI have lead to substantial enhancements in the automation of operations and growth of robotic devices for the mining industry. Mine locations are progressively adopting robotics to stay at the forefront of mining technology. Areas of prolonged focus include advanced analytical tactics to enhance maintenance results and efficiency; location awareness of equipment, and enhanced method automation.
Automation of mining equipment and processes is increasing. Hard-Line is a global company providing the most recent advances in technology to the mining industry. Their Teleop Teleremote Control system allows operation of all heavy machinery via WiFi, ensuring that a higher percentage of the workforce can operation machinery, and allows all mining processes to be interconnected to increase efficiency and productivity.
Computing platforms are required to operate at faster speeds while still being able to operate under the tough conditions at a mining site. New algorithms for signal processing, detection, and control are being currently developed to help raise the safety, accuracy, and efficiency of automated mining operations.
References and Further Reading
Disclaimer: The views expressed here are those of the author expressed in their private capacity and do not necessarily represent the views of AZoM.com Limited T/A AZoNetwork the owner and operator of this website. This disclaimer forms part of the Terms and conditions of use of this website.