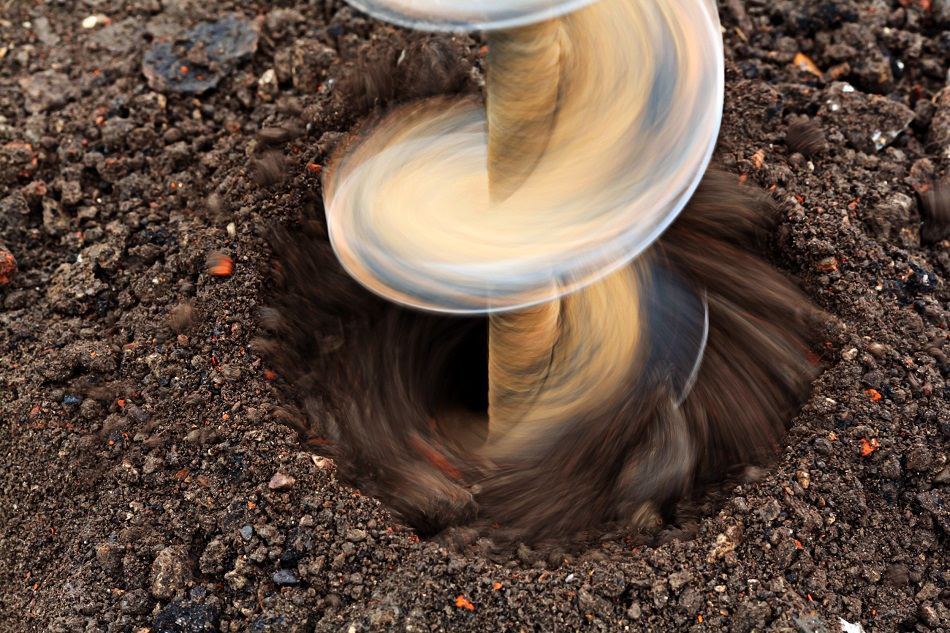
Image Credit: Kickigin/Shutterstock.com
Updated on 17/02/2020 by Brett Smith
The generation of abrasive wear and friction can not only cost an industry a considerable amount of money because of downtime and product replacement, but these common nuisances within the mining industry can also result in reduced life of various parts, increased need for replacement parts, greater operating costs, greater maintenance costs, higher staffing levels for maintenance workers and increased downtime.
It is therefore crucial for the mining industry to utilize validated analytical techniques to estimate, predict, and analyze friction and abrasive wear that is generated on all relevant mining equipment, machinery, and products.
Types of Wear
In mining operations, there are four different types of wear: abrasion, erosion, adhesive wear and surface fatigue. Abrasion wear is caused by hard bits of material being pressed against and grinding along a softer surface. The particles responsible for abrasion typically have sharp angular edges that cut into the softer surface. Erosion is caused by the mechanical interaction between a surface and a fluid that may or may not contain particles. We typically associate erosion with acts of nature, but in mining operations, erosion can be seen when exhaust fans blow dirty air against surfaces.
Wear due to adhesion is caused by the localized bonding between two contacting surfaces. Often, adhesive wear can lead to abrasive wear as particles from the contacting surfaces break off. Surface fatigue is caused by the breaking off of a material due to cyclic stress generated by rolling or sliding action. This type of wear can be aggravated by high temperatures and mechanical wear qualities.
The Cost of Wear
In general, wear costs every industrialized nation approximately 1-4% of their gross national product (GNP).
In addition to being economically costly, wear also increases global energy demand. Currently, the mining and minerals industry accounts for up to 7% of the global energy output, which is largely attributed to the vast amount of electricity used throughout the mine.
The use of other energy sources, including diesel oil fuel, coal, natural gas, and gasoline, also play a significant role in the energy output generated by the mining and minerals industry. The presence of abrasive wear on mining equipment can further increase the energy consumption within this industry, as mining machinery will often require a greater amount of energy to overcome significant friction losses.
Numerical Models
Several different numerical models have been used to approximate the wear generation of machinery when used for several different mining processes, including excavation, comminution, and the transportation of ore.
The methodology behind these numerical models shares a similar foundation where both the particle motion is stimulated and ultimately used to assess and analyze the potential wear that will be generated during the process.
The discrete element method (DEM) and Archard’s wear rule is a unique combination of numerical models widely used throughout the mining industry to predict wear generation on machinery. For example, the DEM-Archard approach has been used to assess and analyze the wear profile of mill liners, which was achieved by obtaining a simulation of the operation of the mill liners to obtain precise experimental values.
Similarly, the DEM-Archard approach was further enhanced by adding a finite element method (FEM) to predict the failure of roadheader picks under a simulation of brittle rock cutting. Smoothed particle hydrodynamics (SPH) has also been used to enhance the DEM-Archard approach to understand the behavior of particles and their contribution to the wear in a dumper truck body.
Microstructure Analysis
In a recent study investigating the impact wear resistance of a novel modified medium manganese steel (MMAS), researchers conducted impact abrasive wear tests to examine wear behavior. Additionally, the morphological features of the impact wear surface were observed by a scanning electron microscope (SEM), whereas the martensitic transformation of the material’s surface was studied by X-ray diffraction (XRD). Transmission electron microscopy (TEM) also allowed the researchers to analyze the microstructure of the impact wear layer.
The SEM, XRD and TEM observations made in the aforementioned paper allowed the researchers to confirm the existence of deformations and dislocations within the microstructure of the MMAS material.
Furthermore, numerical studies were a highly useful and accurate method of predicting wear generation on mining products. Taken together, these two classes of wear generation analytical techniques can provide the mining sector with a plethora of useful information capable of reducing this industry’s energy demand, while simultaneously improving their ability to preemptively overcome the effects of wear on mining products.
Wear Protection Measures
Lubrication and wear protection measures are critical to just about every mining operation. Some basic examples of wear protection measures include rubber lining for conveyor belts, open gear lubricants, wire rope lubricants and lubrication systems.
Tightly attached to a conveyor belt, rubber linings are designed to resist abrasion and prevent corrosion. Due to the extreme conditions of typical mining operations, these linings should be heat and fire-resistant.
Lubricants can be either penetrating, which contain a solvent that delivers lubricant deep into a part or surface, or coating, which seal the exterior of a surface with a thick film. Effective open gear lubricants have significant load-bearing, vibration reduction and water resistance qualities; while wire rope lubricants are made to form a dense film that protects draglines and drag robes from abrasion and corrosion.
Automatic lubrication systems are often used in mining operations to provide localized lubricant in precise amounts at exact moments. Typically made up of a timer, reservoir, pump, lines, pistons and valves, these systems are strategically set up to minimize friction and resulting wear. Valves and pistons allow the system to deliver lubrication at the various necessary locations.
References and Further Reading
- Rojas, E., Vergara, V., & Soto, R. (2019). Case study: Discrete element modeling of wear in mining hoppers. Wear 430-431; 120-125. DOI: 10.1016/j.wear.2019.04.020.
- Holmberg, K., Kivikyto-Reponen, P., Harkisaari, P., Valtonen, K., et al. (2017). Global energy consumption due to friction and wear in the mining industry. Tribology International 115; 116-139. DOI: 10.1016/j.triboint.2017.05.010.
- Ge, S., Wang, Q., & Wang, J. (2017). The impact wear-resistance enhancement mechanism of medium manganese steel and its applications in mining machines. Wear 376-377(Part B); 1097-1104. DOI: 10.1016/j.wear.2017.01.015.
- https://www.mining-technology.com/features/feature93701/
- https://arm.com.au/image/data/25-Brochures%20and%20Cost%20analysis%20thesis/thesis.pdf
Disclaimer: The views expressed here are those of the author expressed in their private capacity and do not necessarily represent the views of AZoM.com Limited T/A AZoNetwork the owner and operator of this website. This disclaimer forms part of the Terms and conditions of use of this website.