Article Updated on 4th February 2021
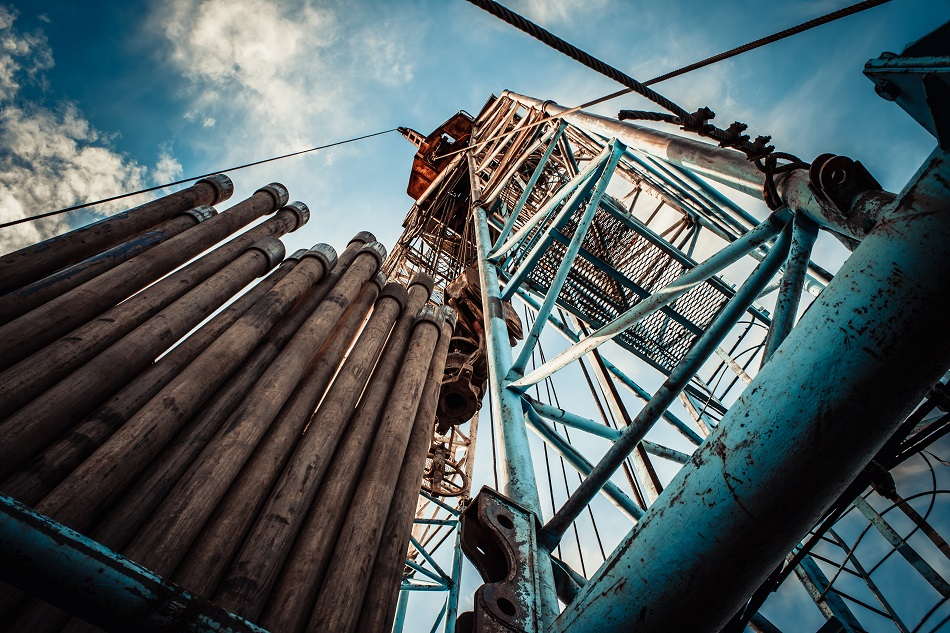
Image Credit: Maximov Denis/Shutterstock.com
Drill rigs are structures that are used to drill wells for water, oil, and natural gas extraction. They can either be massive stationary structures or small enough to be moved by workmen in the field by hand or with the aid of other machinery. Specifications for their construction demand that the materials used in their construction can stand up to rigorous use, loading conditions, and environmental conditions.
Especially when drilling for crude oil, drilling rigs can be exposed to huge stresses and levels of corrosion, which creates massive problems during their operational lifetime, including:
- Acid-bearing fluids can affect the tubing they pass through
- Crude oil, which contains chemical substances such as sulfur and hydrogen sulfide, can elicit corrosion.
- Physical and chemical contaminants from mud and seawater can enter the system
- High temperatures can be generated during operation
All these issues can lead to fatigue in a drilling rig and increase the risk of catastrophic failure. Therefore, the materials used to construct drilling rigs must be able to withstand these conditions. One material which is especially suited to this task is steel, of which there are many types and alloys on the market.
Properties of Steel
Steel is a widely used material in construction and mining. Steel has many important properties that make it suitable for a wide array of applications, the most important being good formability and durability, high tensile and yield strength, and superior levels of conductivity. Another highly important property is its resistance to corrosion.
Steel’s mechanical properties can be selected and controlled during the manufacturing process by the application of processing, heat treatments, and chemical compositions, leading to the final microstructure. Thus, the tensile strength and property values of the finished product that relate to the chosen application can be achieved through these rigorous processes and final testing.
Common additives applied to steel include molybdenum and chromium. These additives enhance the ability of steel to resist corrosion and high temperatures. There are many different types of steel used in drilling rigs.
Stainless Steel
Stainless steel is historically one of the most commonly used types of steel. It contains at least 10.5% chromium, which creates a “passive layer” on the surface of the steel which enhances the corrosion resistance of the steel. Other metals including molybdenum and nickel may be present. Stainless steel is mainly used in structural components, flowlines, and umbilicals.
Carbon Steel
Carbon steel is a type of steel that has improved strength due to the addition of carbon, which typically makes up less than 2% of the finished steel. Carbon steel also contains small levels of phosphorus, silicon, sulfur, and manganese. It is, however, susceptible to corrosion, but, being very strong, it is suitable for structural elements and is also used in flowlines and pipelines. It is the most widely used steel in the oil and gas industry.
Engineered Steel
Also known as special bar quality (SBQ) steel, engineered steel contains nickel, chromium, molybdenum, or carbon. It is used where there is a need for moving parts and mitigates safety and reliability risks, such as shafts, bearings, and drill bits.
Nickel Alloys
Nickel alloys of steel are strong and very resistant to corrosion. Steel with 9% nickel content is tough at extremes of temperature and is therefore used in heat exchangers. These durable alloys of steel are commonly used in “Christmas trees” – the combination of valves and piping which fit over the wellhead.
Inconel
Inconel is a nickel and chromium (up to 70% and 24%, respectively) based superalloy. It is extremely resistant to corrosion, can be used in high temperature and pitting environments, seawater, acid applications, is resistant to mechanical stresses, and comes in various grades. Used in wellhead components, valves, drilling tools, and flare booms, Inconel is a trademark of Special Metals Corporation (PCC Energy Group.) Inconel is expensive to produce due to the difficulty of machining and welding it.
Incoloy
Another trademark of Special Metals Corporation (PCC Energy Group) Incoloy is a more cost-effective alternative to Inconel. This is due to a higher concentration of iron in the superalloy. It is suitable for aqueous environments, process piping, sour gas, and high chloride environments.
Monel
Monel is another corrosion-resistant superalloy produced by the same company that manufactures Inconel and Incoloy. Monel is nickel and copper-based alloy (average 60% and 30% respectively) that is used in pumps, valves, heat exchangers, electrical components, and down-hole equipment.
Hastelloy
Manufactured by Haynes International Inc. Haselloy is an oxidation/corrosion and erosion resistant alloy of nickel and molybdenum. Hastelloy has high mechanical strength, especially at high temperatures. It is commonly used in pumps, valves, heat exchangers, and pressure vessels.
Sources and Further Reading
Disclaimer: The views expressed here are those of the author expressed in their private capacity and do not necessarily represent the views of AZoM.com Limited T/A AZoNetwork the owner and operator of this website. This disclaimer forms part of the Terms and conditions of use of this website.