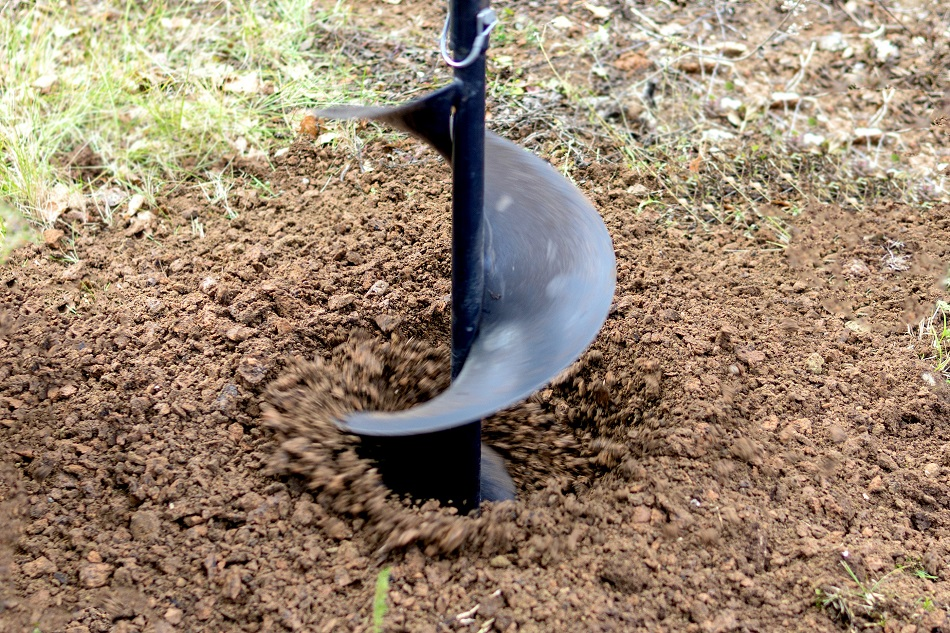
Image Credit: 63ru78/Shutterstock.com
Many different pieces of equipment are utilized in the mining industry for a variety of purposes. One of the tools used worldwide in mining operations is the top hammer drill. Due to the high stresses involved in boring into tough rock faces, top hammer drills need to contain materials that can stand up to these rigors and repeated use.
What is a Top Hammer Drill?
A top hammer drill is a large piece of mining equipment that can easily bore into hard rock surfaces. The internal workings of the drill produce a percussive force on the drill rods and tubes, which is transmitted to the drill bit. Much like a hammer drill, a top hammer drill effectively drills from outside the hole.
Top hammer drilling simultaneously uses four active elements to drill a hole; feed force, rotation, percussion, and air. Feed force keeps the bit in constant contact with the bottom of the hole. Rotation of 100rpm or greater ensures that each successive blow impacts the surface in a different orientation. Up to 2500 percussive forces per minute transmit an energy wave, fracturing the ground through impact force. Finally, compressed air is used to eject any excess material (chippings) from the hole.
Steel
Due to the working conditions during their operation, top hammer drills need to utilize materials that can stand up to these rigors. One material that is particularly suited to this task is steel.
Steel is a widely used material in the construction and mining industries due to its important properties. These include good durability and formability, superior tensile and yield strength, resistance to corrosion, and high conductivity. The mechanical properties of steel are selected and controlled during its manufacture via rigorous application of processes such as heat treatment which leads to the final microstructure desired.
Typically, steel is strengthened by the addition of other substances including carbon, nickel, chromium, and molybdenum.
Drill bits can be coated with other materials including tungsten carbide to make them even stronger and less prone to failure due to impact and stress. Aside from the drill bits themselves, steel is used in the construction of moving parts including bearings, and the steel used must be able to stand up to the stresses on these parts to avoid catastrophic failures in the operation of the machinery.
- Carburized steel – Used in drill bits due to its high strength. Carburizing steel involves adding carbon under high temperatures to create case-hardened steel able to withstand high amounts of stress. Many different grades of carburized steel are used and this type of steel is suitable for repeated use.
- Chromium-nickel alloys – Alloys of steel including relatively high concentrations of nickel and chromium (such as Inconel and Incoloy) have superior strength. This makes them especially suitable for drill bits and components that undergo a lot of stress during operation.
- Through-hardening steel – Heat-treated steel containing a relatively high concentration of carbon. Typically used in moving parts including bearings and diesel injection components that require high fatigue strength due to its high strength but tendency to fracture under impact or shock loads.
- Cromax – Chrome, and nickel-chrome plated steel bars. Used for piston rods in hydraulic cylinders.
- General structural steel – Used for casings and general structural elements.
- Nitriding steel – Nitrogen-infused steel with a case-hardened surface. The heat treatment process is performed at a lower temperature than carburizing. Nitriding confers increased corrosion resistance, and the use of this type of steel is typically for small gears and crankshafts.
Sources and Further Reading
Disclaimer: The views expressed here are those of the author expressed in their private capacity and do not necessarily represent the views of AZoM.com Limited T/A AZoNetwork the owner and operator of this website. This disclaimer forms part of the Terms and conditions of use of this website.