Welding Alloys offers a range of welded overlay plates in both standard and complex carbide models. The welded overlay plates have wear-resistant characteristics that considerably exceed those of tempered and quenched abrasion-resistant steels.
Such exceptional properties are obtained by the formation of very fine and uniformly distributed chromium as well as complex carbides across the thickness of the welded layers.
Advanced equipment and in-house developed technology make sure that Welding Alloys’ products are distinguished by their:
- Functionality
- High-quality consistency
- Uniform appearance
- Homogeneity across the welded deposit thickness
- Ability to be cut, formed, and welded to create fabrications—this is realized by using low carbon structural steel as the base material for all overlay materials from Welding Alloys
Apart from abrasion resistance, Welding Alloys also supplies materials that are specially developed to resist material loss induced by corrosion, high temperatures, high impact, and also a combination of all these wear mechanisms.
Hardplate™
This is a heavy-duty composite overlay wear plate.
- A choice of numerous overlay materials are available based on the wear mechanisms present and the area of use
- The overlay thickness and base material are chosen according to the type of application
- The desired solution for maintaining the wear areas
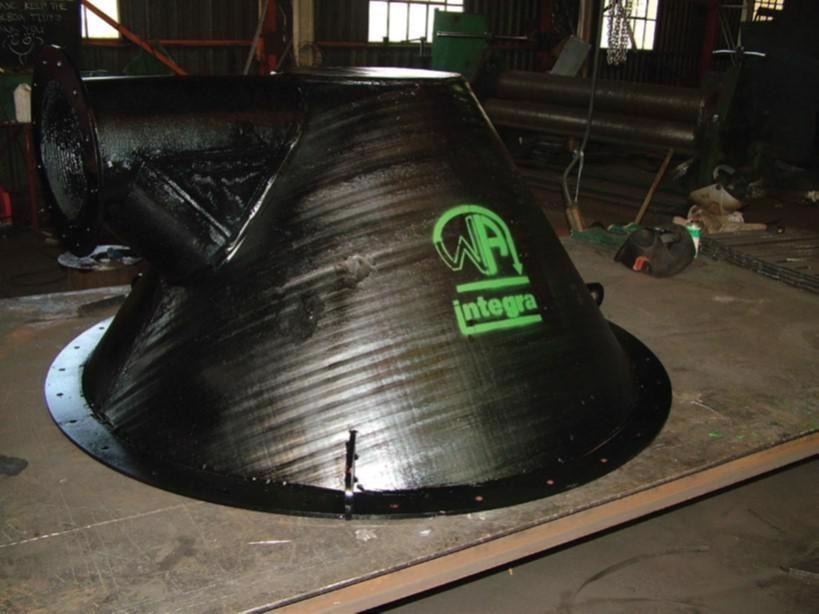
Image Credit: Welding Alloys Ltd
Hardlite™
This is an ultra-thin welded overlay wear plate that has less than 5 mm overall thickness.
- Perfect for high-wear areas, where weight limitations apply
- Excellent hardness yet easily formable
- Extremely lightweight, making it well-suited for wear protection of moving parts, for example, fan blades
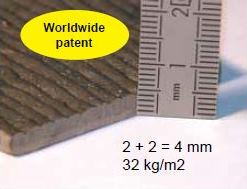
Image Credit: Welding Alloys Ltd
Tuffplate™
This is an impact-resistant composite overlay wear plate.
- Perfect for areas of material transfer and transportation
- Can be used in high-impact areas, both with and without the addition of abrasion

Image Credit: Welding Alloys Ltd
Welding Alloys offers overlay products that come in a wide range of thicknesses and are well-suited for all application requirements. Tuffplate™, Hardlite™, and Hardplate™ are offered in both standard dimensions and cut-to-size configurations.
Welding Alloys also provides design and fabrication services across its international network of Integra workshops. In addition, technical and application data sheets are also provided on request.
Table 1. Source: Welding Alloys Ltd
HardplateTM 100 |
HardplateTM 300 |
HardplateTM 600 |
HardliteTM |
TuffplateTM |
Chromium Carbide based product
Excellent abrasion resistance
Optimum solution for most applications
Low-range temperature resistance |
Consists of Chromium and Niobium carbides
Improved wear resistance
Excellent for use in high abrasion applications
Moderate temperature resistance |
Carbide structure consists of a variety of complex carbides
Superior wear resistance
Excellent for use in areas of wear at elevated temperatures |
Refined welding techniques to ensure ultra-hard, very thin overlay
Fine, densely packed chromium carbides in an austenitic matrix
Best suited for low impact, high abrasion applications where there are weight restrictions |
Finely dispersed carbides embedded in a tool steel matrix
Ideally suited for areas of high impact, pressure, and abrasion or a combination of these mechanisms |
Fair corrosion resistance
Designed to withstand moderate impact |
Fair corrosion resistance with low levels of impact resistance |
Moderate levels of abrasion resistance with high impact resistance |
Hardness
62-64 HRC |
Hardness
60-62 HRC |
Hardness
62-64 HRC |
Hardness
64-66 HRC |
Hardness
52-55 HRC |
Hardness values are obtained from three-layer deposits
Table 2. Standard dimensions. Source: Welding Alloys Ltd
Type |
Size |
Hardplate™ |
1500 x 3000 mm
2000 x 3000 mm |
Hardlite™ |
1000 x 2000 mm |
Tuffplate™ |
1500 x 3000 mm |
Other dimensions are available on request
Table 3. Standard thickness. Source: Welding Alloys Ltd
Type |
Base Plate |
Overlay |
Hardplate™ |
5 – 15 mm |
3 – 15 mm |
Hardlite™ |
2 – 3 mm |
2 - 3 mm |
Tuffplate™ |
5 – 10 mm |
3 – 8 mm |
Other thicknesses are available on request
Welding Alloys Group understands that each requirement is unique and that all off-the-shelf products are not suited to meet its customers’ requirements, all the time. Therefore, the company also provides customized overlay solutions to fulfill specific requirements and conditions. For example, these could be stainless steel overlays on carbon steel, or wear-resistant overlays on stainless steel, heat-resistant steels, or wear-resistant steels.
Welding Technology
While developing the composite overlay material at Welding Alloys, great emphasis is placed on the regulation of dilution and cooling rates. High dilution ratios can also have an impact on the final weld chemistry, and while hardness may still be in the satisfactory range, the weld metallurgy will not reflect the same acceptable range. In essence, hardness is not a direct measurement of wear resistance and must only be employed as a guideline when investigating the hardfaced overlay plate.
ASTM G-65 Wear Test (independent laboratory). The graph above reflects results from ASTM G-65 wear testing performed by an independent laboratory. The results compare the wear life of various products tested. As an example, Hardplate™ 100 has outlasted 500 BHN quenched and tempered material by a factor of 4 and Hardplate™ 300, by a factor of 7. Image Credit: Welding Alloys Ltd
Welding Alloys has also designed advanced automated welding equipment with the help of suitable welding processes and specialized welding consumables to make sure that weld metallurgy is at its optimum and dilution is kept to a minimum. This ensures maximum possible carbide levels that are distributed across the whole thickness of the overlay.
Most of the plate products offered by Welding Alloys are created using both stinger and oscillated bead methods. These two welding techniques have been refined to create overlay composition as well as weld metal metallurgy that favors the formation and distribution of carbide across the overlay thickness.
Manufacturing and Plate Processing
For additional information on plate cutting, forming, processing, welding, fitment options, etc., customers can refer to Welding Alloys’ detailed Workshop and Plate Processing Manual available on request.
All plate products offered by Welding Alloys can be thermally processed using plasma or laser cutting methods and can be joined through welding.
These thermal processes do not have any impact on the wear resistance in the heat-affected zone and effectively remove preferential wear that is often observed in such areas when tempered and quenched materials are employed.
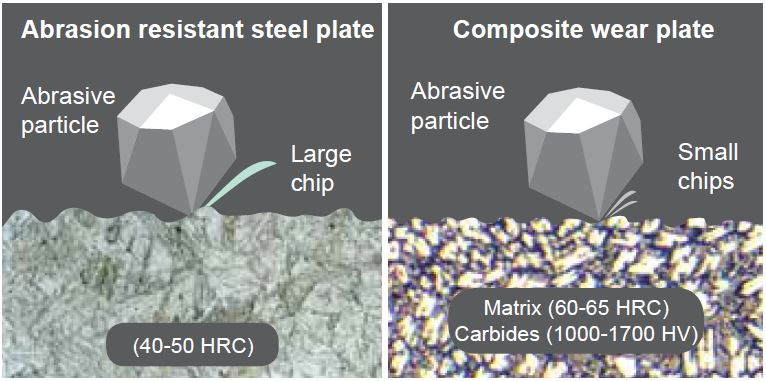
Comparative wear test. Image Credit: Welding Alloys Ltd
Example of Applications
- Truck tray liners
- Hoppers
- Pipes and pipe bends
- Cyclones and classifiers
- Fan blades and casings
- Dust extraction
- General wear liners
- Conveyor liners
- Mixers and mixer blades
- Screens and grids
- Chutes
- Mills and mill liners
- Impact zones
- Slurry systems
- Furnace chutes
- Scrapers
Principal Industries
All products from Welding Alloys are used across the world in various applications and industries, where material loss is caused by wear. Examples of these sectors are given below:
- Cement
- Dredging
- Steel
- Petrochemical, oil and gas
- Mining and quarries
- Public works
- Glass and ceramics
- Recycling and waste incinerators
- Paper and pulp
- Agriculture and forestry
- Power
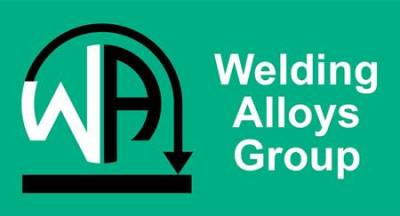
This information has been sourced, reviewed and adapted from materials provided by Welding Alloys Ltd.
For more information on this source, please visit Welding Alloys Ltd.