The automotive industry has been developing self-driving vehicle concept cars for some years now, but the complexities of autonomous driving in unpredictable environments have so far made widespread adoption in transportation unattainable. The more predictable environments that vehicles must traverse in mining operations mean that this industry is better poised to put self-driving vehicles to use.
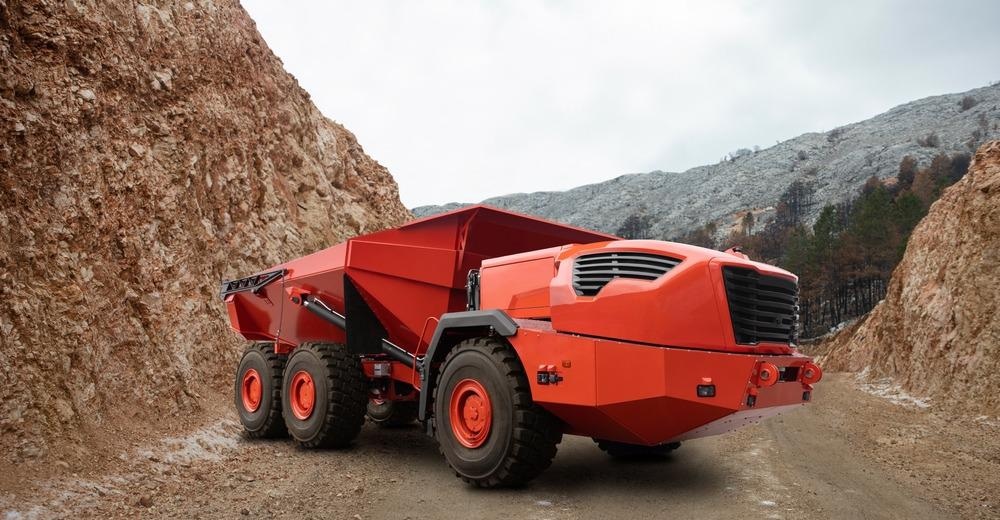
Image Credit: Scharfsinn/Shutterstock.com
Autonomous vehicles are already beginning to appear in some leading mining operations around the world. Chinese mining firm SANY, for example, recently announced its deployment of two electric-powered autonomous mining trucks.
The SKT90E mining trucks deployed by SANY come equipped with advanced capabilities for environmental identification and independent positioning. The truck can also complete route tracking, loading, unloading, and parking operations independently of human control.
A BHP mine in Western Australia has been employing a fleet of fully autonomous mining trucks since 2017, and BHP is beginning to introduce the system to its other sites as well.
Global mining firm Rio Tinto is now operating more than 130 autonomous mining trucks across its entire inventory. The company’s iron ore mines also operate with a completely autonomous, heavy-haul long-distance railway system.
Rio Tinto’s Pilbara mine has recently transformed operations by deploying over 80 autonomous trucks in roaming, digging, excavating, and transportation operations around the massive site.
The mine is also spearheading innovative solutions to workforce displacement from introducing autonomous technologies. The 12,000 workers employed there remained on the payroll, with many employees being retrained and retained in the company’s control room 750 miles away.
The operations center near Perth Airport can now supervise autonomous operations at the Pilbara Site, with workers coming on-site only when required for maintenance or safety checks.
Another mining giant, Vale, is using autonomous mining trucks at its Carajas iron ore complex in Brazil. Carajas is Vale’s largest iron ore mining facility, and the company’s introduction of autonomous vehicles here has been a strong signal of the industry’s move towards more autonomous technology.
Vale predicts it will increase productivity and decrease operational risks with the introduction of the driverless fleet. There are currently six vehicles in operation at the site, capable of transporting up to 320 tons of iron ore in its impressively large frame (three times as wide as an average mining truck).
What are the Benefits of Self-Driving Vehicles in Mining?
Mass production and consumption are some of the pillars of the global economy, and it requires the extraction of raw materials from mining operations.
It will be necessary to limit this rampant extraction in the coming years to meet our climate and environmental goals because it destroys local habitats, consumes huge amounts of energy, and leaves heaps of pollution and waste in its wake.
However, it will also be necessary to continue to mine for certain earth materials – particularly metals such as copper – to decarbonize our economies and switch to fully renewable energy.
Against these constraints (limiting the environmental damage of extracting raw materials; while needing raw materials to limit other kinds of environmental damage), mining is also approaching another major problem: dwindling resources. Mining firms will increasingly need to work in extreme, inaccessible sites as the finite supply of raw materials in the earth inevitably depletes.
Because of all of this, the mining industry is faced with increasingly diminishing returns on its investments. Limiting costs and increasing productivity are becoming ever more important in the sector.
Leading mining companies around the world are looking to self-driving vehicles to help alleviate many of these problems.
Autonomous mines can operate in extreme conditions without impacting worker safety. They can also operate in remote locations with no local amenities month after month without any need for respite. Centralized control centers in areas that human workers prefer to live can oversee mining operations from any isolated or dangerous site in the world.
Autonomous systems can also help mines to drive productivity up. They can operate around the clock if required, and AI systems can be employed to maximize efficiency in their routes, charging cycles, loading time, and so on.
Autonomous mining could also save mining companies in labor costs. However, companies that have monopolized employment in some communities have a responsibility to look after those communities. Mining companies should look to retrain and retain workers displaced by autonomous operations, as Rio Tinto did in its Pilbara mine.
References and Further Reading
Frangoul, A. (2020). Mining looks to electric, autonomous vehicles to reduce costs and improve efficiency. CNBC. Available at: https://www.cnbc.com/2020/07/16/mining-looks-to-electric-autonomous-vehicles-to-improve-efficiency.html.
Pilkington, B. (2021) Driving Sustainability Forward in Mining with Electric Vehicles. AZO Mining. Available at: https://www.azomining.com/Article.aspx?ArticleID=1580.
Robinson, D. (2019). How autonomous technology could make mining safer, cheaper and more valuable. NS Energy. Available at: https://www.nsenergybusiness.com/features/autonomous-mining-technology-zyfra/.
Vale’s self-driving trucks gear mining towards the future. (2021) Minging Global. Available at: https://miningglobal.com/automation-and-ai/vales-self-driving-trucks-gear-mining-towards-future.
Disclaimer: The views expressed here are those of the author expressed in their private capacity and do not necessarily represent the views of AZoM.com Limited T/A AZoNetwork the owner and operator of this website. This disclaimer forms part of the Terms and conditions of use of this website.