Mining is undergoing something of a radical technological shift, the likes of which have never rocked the typically conservative industry before. Widespread trends such as the adoption of automation technology, electrification, and digitalization have also been sped up by the onset of COVID-19.
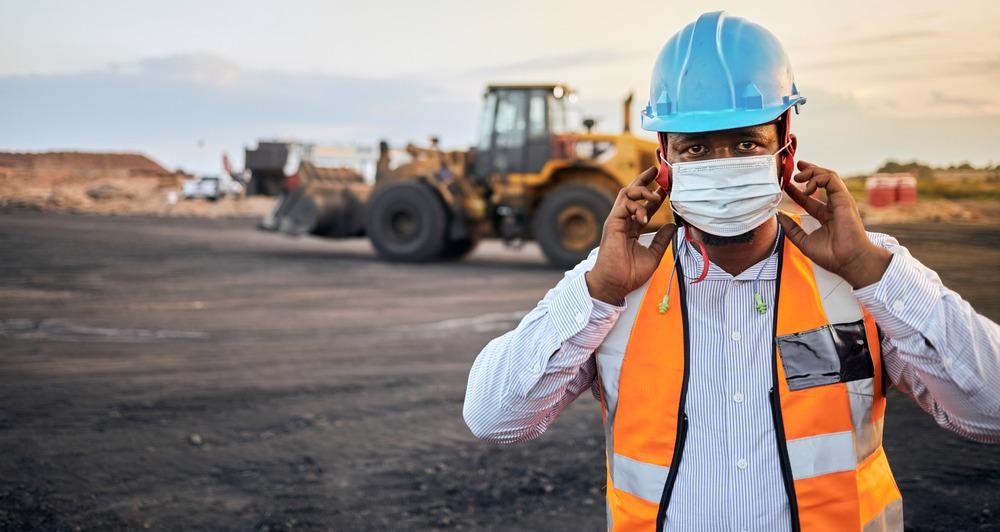
Image Credit: Magnifical Productions/Shutterstock.com
COVID-19 has predominantly impacted supply chains and on-site efficiency in the mining industry. Transporting materials away from the mine has been difficult, as well as transporting components, machinery, and other resources to the mine.
Lockdown measures and measures put in place to prevent people from spreading the virus also impacted on-site efficiency, as workers’ shift patterns became more unreliable and many mines were forced to temporarily close down. Mining operations extracting residual resources were highly impacted in this way.
The highest impact from COVID-19, however, was in pre-mining activities such as feasibility studies and projects for developing new mines. This was mostly due to restrictions on international and regional travel. Exploration and discovery stage projects were impacted in a similar way, although this did not affect the mining industry as much.
In the medium term, the industry is expected to withstand these impacts fairly well. There has continued to be demand and capacity for maintaining more mining production than was expected since COVID-19. This was due mainly to a steady demand for raw materials in China, negating the effects of reduced demand elsewhere in the world.
The long-term impacts of COVID-19 on mining are yet to be fully understood, however. The impact of break-in exploration and development projects in 2020 and 2021 may be years down the line.
How is Mining Responding to the Impact of COVID-19?
In some ways, COVID-19 is simply speeding up the mining industry’s wide adoption of new technologies. Pioneering firms have embraced automation and digitalization for some years now, and the restrictions of operating under COVID-19 have also convinced many more companies in the traditionally conservative industry.
Changes such as new recruitment strategies and a stronger focus on sustainability show the mining industry responding to different values and motivators in today’s economy. This difference is also impacted by COVID-19, especially regarding people’s desire to work remotely or with flexible hours.
Automation and Digitalization
With rapid technological advances in the fields of sensors, machine learning (ML), artificial intelligence (AI), and robotics, automation has been increasingly applied in mining operations. Autonomous vehicles, machinery, data centers, and planning functions have all been introduced to increase site productivity.
COVID-19 sped up the adoption of automation technologies in mining. Facilities finished autonomous transformation projects ahead of schedule as their workers were unable to get to the site.
Some companies have retrained and retained their workforce in desk-based operations, supervising autonomous mines remotely.
In general, mining has increased its use of data and ‘digital twinning’ systems, where mining sites are linked to centralized control centers in big cities. The big three iron ore mining firms in Australia have all adopted the digital twins approach in recent years. AI combs through the data collected at mining sites and creates models, blast timings, and many other optimizations for the on-site work.
Recruitment and Skills are Changing
The trends toward automation and digitalization in mining (both sped up by COVID-19) require a new set of skills for workers in the mining industry. Data science, systems and control engineering, software development, and digital infrastructure that mining uses today are beginning to change how the industry approaches recruitment and skills.
Some mining firms have retrained their workers who would be displaced by automation and retained them in new desk-based roles. Others are looking to non-mining sectors to find top digital talent.
The key to attracting this non-traditional mining talent will be improving the image of mining, especially when it comes to worker rights and sustainability. Moves to secure employment for displaced employees in new desk-based roles will certainly benefit mining firms looking for new talent as well.
Similarly, acting on their own commitments to decarbonizing operations and extracting materials in a more environmentally responsible way will enable mining firms to attract top new talent from other sectors and industries.
Mining is also considering its talent pipeline through education and university. Changes to degree curricula could train mining engineers with the digital technology skills needed for the modern mining industry. Working with educators in traditional computer science and digital technology programs could also help mining to attract graduates in this highly competitive recruitment market.
References and Further Reading
Galas, A. et al. (2021) Impact of Covid-19 on the Mining Sector and Raw Materials Security in Selected European Countries. Resources. Available at: https://doi.org/10.3390/resources10050039
Robinson, B. (2021) 4 Ways Mining is Changing in 2021. CM Industrial. Available at: https://www.searchingindustrial.com/media/1100/4-ways-mining-is-changing-in-2021
Disclaimer: The views expressed here are those of the author expressed in their private capacity and do not necessarily represent the views of AZoM.com Limited T/A AZoNetwork the owner and operator of this website. This disclaimer forms part of the Terms and conditions of use of this website.