Workers face numerous hazards in underground mines, ranging from structural collapse to flooding and explosions. One of these hazards is dust, created in tremendous amounts by different mining operations. Techniques for controlling dust in mines exist to keep workers safe. Novel approaches utilizing cutting-edge technology have been proposed in recent years.
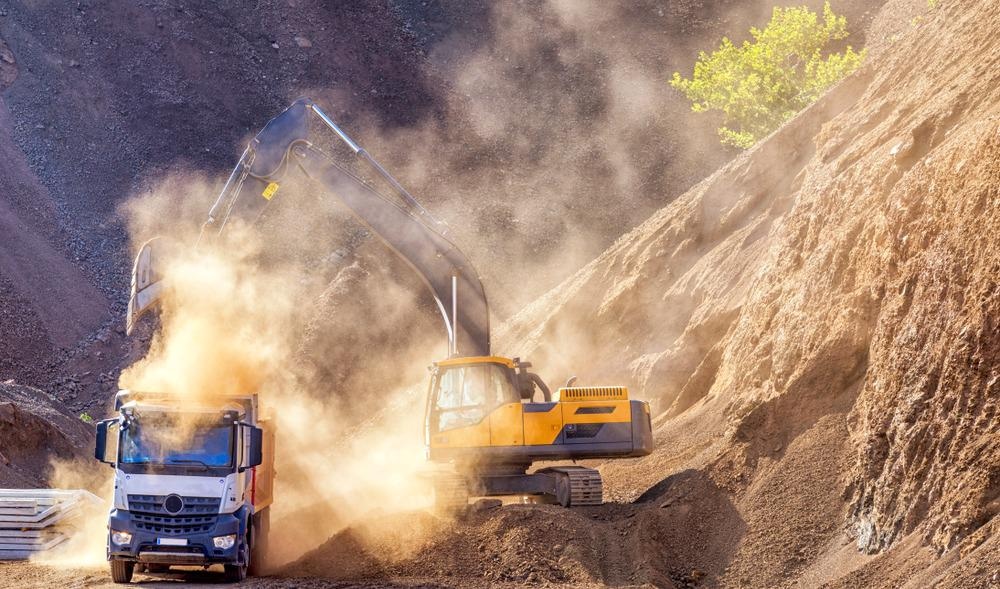
Image Credit: Funtay/Shutterstock.com
Controlling dust is challenging. Most methods only yield 25-50% reductions in breathable dust, which is often not enough to achieve dust compliance standards. Therefore, mine operators often use several dust control methods simultaneously and may not even know which methods are effective or not. This is compounded by a 25% error in dust sampling and 50% day-to-day variations in dust generation in the same mine.
Nevertheless, some consensus has emerged over which methods are most effective for dust control. These fall into three major categories: ventilation, water, and dust collecting. Preventative strategies such as minimizing the amount of disruption and breakage required can also be highly effective.
Ventilation in Mine Shafts for Dust Control
Ventilating the air in mine shafts both dilutes and displaces harmful dust particles. Ventilation systems dilute dust clouds with clean air, reducing the concentration of dust. Dust is displaced when the ventilation system maintains a high enough air velocity to reliably keep dust downwind from workers.
Ventilation systems dilute dust in proportion to an increase in airflow. Increasing airflow can be significantly expensive and often poses substantial technical challenges. Air moving through ductwork or shafts at speeds of 1 km/minute or more is particularly challenging to dilute with increased airflow.
Displacement ventilation uses airflow to confine the dust source and keep it away from workers, reliably blowing dust downwind. Continuous miner faces and tunnel boring machines on exhaust ventilation use displacement ventilation in mines. Enclosing a dust source, a transfer point between conveyor belts for instance, and extracting the dusty air from the enclosure is another example of displacement ventilation.
Displacement ventilation is difficult to implement. When workers are three to five meters from a dust source, a substantial air velocity is required to keep dust downwind, up to 50 m/minute. In underground mines, there may not be enough air available to achieve velocities like this.
Two techniques are used to overcome this challenge. The first is reducing the cross-sectional area of the air course between the dust source and workers. This raises the air velocity, keeping the dust source confined. Second, reducing turbulence in the dust source reduces eddy currents that push dust upwind toward the worker. Less turbulent dust sources require less air to confine the dust clouds they generate.
Ventilation techniques, particularly displacement ventilation, are the most effective dust control strategies for keeping workers safe.
Capturing Airborne Dust Particles with Water Spray
Water is used to wet broken material in various stages of the mining operation and to capture airborne dust particles. Wetting broken material is much more effective than airborne capture, which has a negligible effect on worker safety.
Most dust particles created when minerals and ground material are broken up are not released into the air. Instead, they remain attached to the broken material’s surface. Wetting the broken material keeps the dust particles attached to the surface, preventing them from becoming airborne.
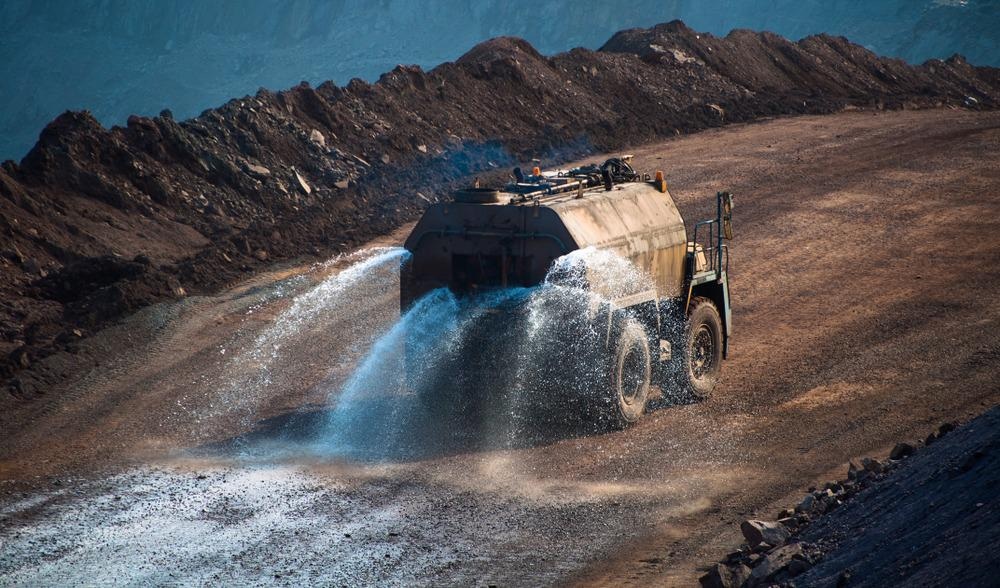
Image Credit: Yevhen 11/Shutterstock.com
Excessive moisture levels lead to problems with materials handling, product quality, and operations management. Excessive water use is also one of the ways that mining damages the environment, both as a resource-intensive consumer and a polluting waste generator.
Ensuring that broken material is moistened uniformly can help to ensure effective dust control. To do this, some operations release water at the cutting picks of rotating shearer drums, instead of spraying water from the shearer body. This mixes water in with the material as it is being broken.
As most mechanical mixing takes place during the breakage process, it is best to wet the material at this point to achieve uniform consistency. Wetting material early in the mining process also means that benefits carry over to downstream processes.
More nozzles at lower flow rates are better for achieving uniform wetting. Correctly aiming the nozzles at the broken material – rather than just spraying water into the air – also makes better use of water resources.
Mines looking to improve dust control with wetting should consider upgrading and improving spray operations to ensure broken material is evenly saturated with minimal use of water.
Adding automation to spraying systems can also make them more efficient. Systems such as the NSECO DustPro Spray, featuring 200 psi pressure operation and remote electronic control are well-suited to integration with modern, automated mining infrastructure.
Dust Collectors for the Mining Industry
Low-volume filtration systems such as the Dustcontrol AB’s DC 1800 are used for mining machinery cabs, while high volume dust collectors like the ILMEG HAC 2000 used on asphalt milling machines operate with the same principles on a much larger scale.
The efficiency of any dust collection system is the filtration efficiency of the unit multiplied by its inlet capture efficiency. Filtration efficiency is usually designed to be relatively high, between 90-95%, while inlet capture efficiency can be much more variable. Inlet capture efficiency is 80% or more when the system is extracting air from an enclosed space.
References and Further Reading
Kissell, F.N. (2003). Handbook for Dust Control in Mining. CDC. Available at: https://www.cdc.gov/niosh/mining/works/coversheet1041.html.
Pilkington, B. (2021). The Electric Revolution: The Importance of Global Mining Electrification. AZO Mining. Available at: https://www.azomining.com/Article.aspx?ArticleID=1595.
Tailoring the best solutions for dust control. (2021) Australian Mining. Available at: https://safetowork.com.au/tailoring-the-best-solutions-for-dust-control/.
Wayne, G. (2020). Best Practices for Dust Suppression in Underground Coal Mines. Parker Conflow. Available at: http://blog.parker.com/best-practices-for-dust-suppression-in-underground-coal-mines.
Disclaimer: The views expressed here are those of the author expressed in their private capacity and do not necessarily represent the views of AZoM.com Limited T/A AZoNetwork the owner and operator of this website. This disclaimer forms part of the Terms and conditions of use of this website.