Non-destructive testing can be defined as various techniques that analyze and evaluate the state, integrity, or properties of materials, systems, components, or equipment without damaging the test subject collectively or individually. Mining is an intense industry that uses many different types of heavy equipment and machinery which is likely to cause fatal accidents if not subjected to safety testing.
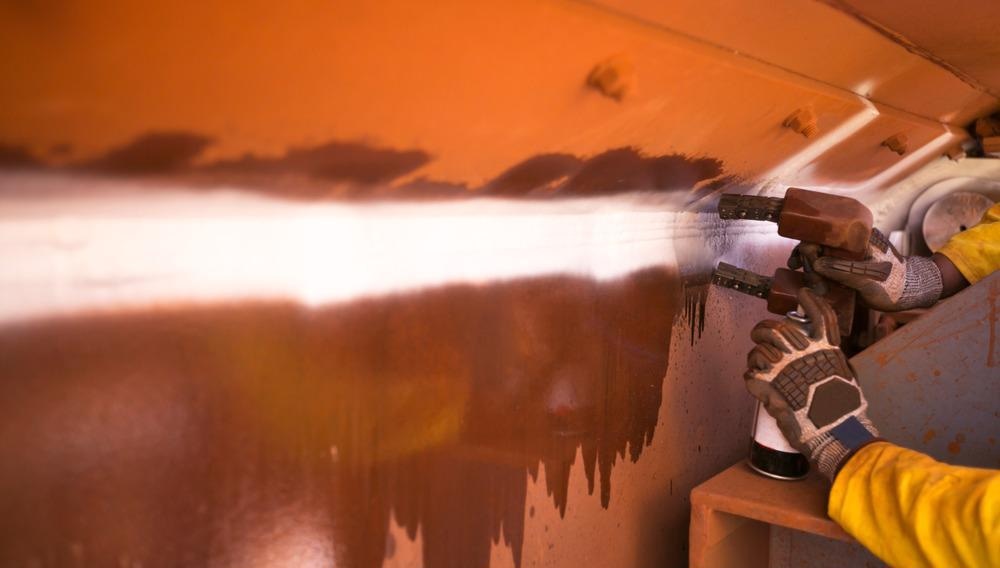
Image Credit: King Ropes Access/Shutterstock.com
Applications of Non-Destructive Testing in Mining
Non-destructive testing can span from the manufacturing of concrete and timber to mining, quarrying, and other activities which rely on lifting heavy loads in daily operations with the help of machinery such as cranes and forklifts.
The frequency at which mining equipment is tested is often mandated by either state or government regulations that certify and give certificates and licenses to operators and equipment to be used in the mining industry until another test is required for its continued use.
The test includes the rate at which the equipment is used and the possible risk to human life. Depending on testing purposes, the frequency of NDT varies from six months to several years.
If equipment is not adequately tested, the machinery or equipment is prone to frequent malfunction or severe damage, which can lead to serious consequences such as injury, fatalities, loss of production time, and more costs as a result of lengthy repairs or replacement of machinery or equipment.
Another aspect of the failure to test for mining equipment can include legal repercussions which attract hefty fines or penalties, or the suspension and revoke of licenses.
Common Types of NDT in Mining Equipment
Automated ultrasonic testing (AUT)
AUT consists of a motorized inspection system known as a scanner. The scanner is responsible for manipulating the probes while simultaneously tracking their position. This method is ideal for welding inspection as well as for corrosion detection in areas that are difficult to access.
There are many benefits of using ultrasonic testing, including:
- It can be employed to analyze unique and complex shaft geometries at a much faster rate when compared to other NDT techniques.
- It also has a higher probability of detecting defects and is more dependable
- It can penetrate the internal structures without the need to disassemble the subject equipment such as pipes and pressure vessels, saving costs and time.
Magnetic particle testing (MPT)
Magnetic particle testing or magnetic particle inspection (MPI) is an NDT technique used to detect cracks and distortions on ferromagnetic and electricity-conducting materials.
The technique uses magnetic fields to check for any discontinuities near the surface of the subject material by having the magnetic field indirectly or directly induced, revealing any surface or subsurface discontinuities caused by leakages in the magnetic flux.
After the subjected component is cleaned of its impurities, dry or suspended ferrous particles are applied to the test subject and are attracted to the area of flux leakage forming what is known as an indication to be detected by specialized equipment. This will enable a decision to be made as to whether the component of equipment is safe to use.
MPT has some very important benefits to the mining industry, including:
- It is a relatively quick and uncomplicated way to detect surface or subsurface defects and reveals the results immediately.
- This method can be easily adapted for workshop use or at the site of interest.
- It is relatively inexpensive compared with radiography.
- It enables both small and large areas of examination and will not require pre-cleaning.
Time of flight diffraction (TOFD)
This technique is based on the time spent by ultrasonic waves or its time of flight and the diffraction that is produced by the extremities of discontinuities.
It consists of two transducers placed on angled wedges to produce longitudinal waves. The two probes in the TOFD machine face each other while the other is received at a known or defined distance to ensure coverage of the desired zone.
Time of flight diffraction is known for its high levels of precision and accuracy. It also includes a live display of the results and only requires a single scan to cover a weld’s complete volume with high levels of sensitivity.
Future of Non-Destructive Testing
Non-destructive testing methods are an extremely valuable aspect of the mining industry and have the potential to improve the efficiency of mining projects.
NDT techniques previously required highly-trained specialists to use these techniques, but recently, automated processes have developed over the past decades and databases have been used to significantly aid the process.
Knowledge of stress factors and material is of particular interest in the mining sector, and it has been acquired with the help of NDT which will be employed even more as new challenges arise.
References and Further Reading
Sutcliffe, D.A. and Cottier, J.A., 1978. Successful applications of ndt techniques to mining equipment maintenance. NDT International, 11(3), pp.135-137
Nucleom. n.d. Ultrasonic Testing | Non-Destructive Testing | NDT Solutions | Nucleom. [online] Available at: https://nucleom.ca/en/nde-solutions/ultrasound
Buffalo Inspection Services. n.d. NDT Inspection Services for Mining Industry. [online] Available at: https://buffaloinspection.com/our-expertise/mining/
Davey, Reginald. 2020. Monitoring Mining Equipment with NDT. AZoMining, viewed 21 January 2022, https://www.azomining.com/Article.aspx?ArticleID=1550
Disclaimer: The views expressed here are those of the author expressed in their private capacity and do not necessarily represent the views of AZoM.com Limited T/A AZoNetwork the owner and operator of this website. This disclaimer forms part of the Terms and conditions of use of this website.