Modern mining is becoming a more connected, data-driven, efficient, and sustainable environment, utilizing several next-generation technologies and techniques to solve key critical issues. This article will look at predictive maintenance and Dingo’s real-world applications and solutions.
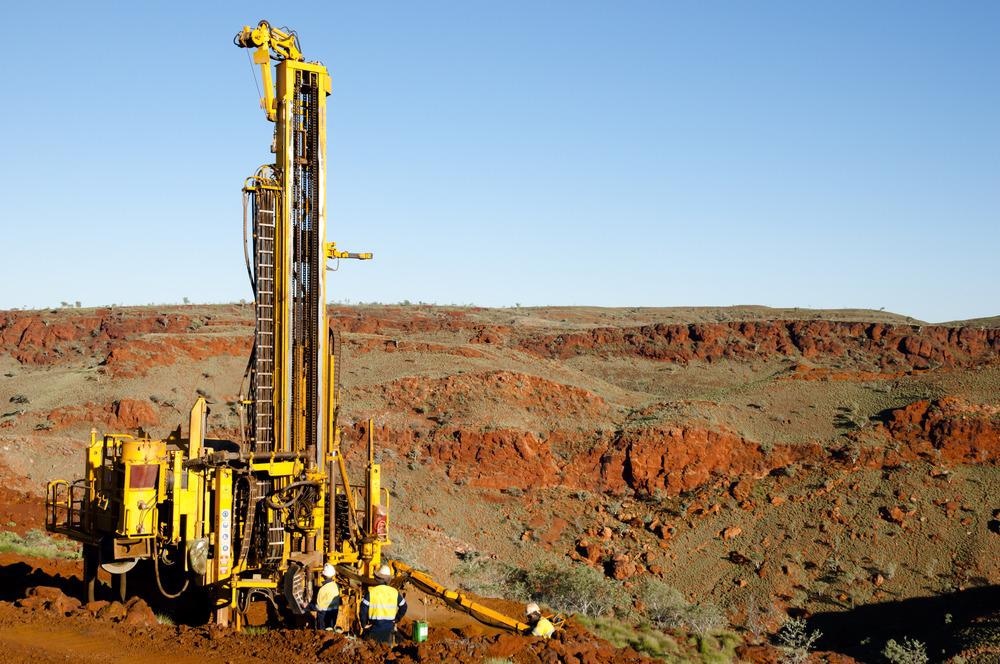
Image Credit: Adwo/Shutterstock.com
Predictive Maintenance in Mining: An Overview
Monitoring heavy equipment in mining keeps it in prime condition for efficient operation. Predictive maintenance, a data-driven technique, helps mining engineers anticipate errors before they occur. While traditional maintenance is still necessary for day-to-day operations, predictive maintenance use is increasing.
Much like predictive analysis uses data to anticipate energy usage and market movements, data analytics are used in predictive maintenance in mining to anticipate failures in equipment and processes. The technique has three main elements:
- Connected devices and sensors
- Cloud computing and software
- Predictive models
As a proactive maintenance methodology, predictive maintenance techniques include infrared thermography, acoustic monitoring, and vibration analysis. Predictive maintenance reduces downtime and overall costs as equipment only needs to be shut down before a fault occurs, but the cost of installing monitoring equipment can be high, as well as the expertise in interpreting data.
Dingo’s Predictive Maintenance Solutions
Dingo, based in Brisbane, Australia, provides solutions for predictive maintenance in mining. With over 30 years of experience, the company currently manages the operational health of over $13.5 billion of heavy equipment. Its expertise and technical solutions are utilized by companies in mining, rail, oil and gas, and wind power. Powerful insights are provided by the company for monitoring heavy equipment in mining by multiple companies worldwide.
The company’s expertise has generated cost savings of over $1 billion for the companies it works with, and its innovative solutions improve profitability, productivity, and performance. The company manages 170,000 components daily.
Trakka Predictive Maintenance Software
Trakka® is a single platform solution that helps companies manage, analyze, and act upon asset health data. It provides teams with tools, insights, and decision support for their asset health programs. It uses real-life data to provide real-world results. The proprietary algorithms and statistical models use failure data from real-world operations which are fed into the system and validated by experts. The company states that it delivers end-of-life accuracy of over 85%.
Easy to integrate with existing IT and systems infrastructure, the Trakka® predictive maintenance software contains many features. These include a field inspection app, direct or parallel ERP integration, customizable dashboards and reporting, financial tracking, workflow management processes, a rules-based decision-making engine, and a data connector library. It also provides visibility and access for unlimited users across all aspects of the business.
Dingo’s Asset Health Manager App
The Trakka® app consists of Trakka® InsightsTM and Trakka® InspectTM which enables users to both see and track equipment health and inspect and report system conditions in the field whilst using a mobile device. It provides real-time predictive data analytics and actionable inspection solutions for data capture and analysis. The app has both online and offline functionalities.
Features of the app include ease of use, broad visibility, standardized evaluations, data utilization, and actionable insights. The app is easily integrated into existing ERP systems and allows uploaded data to be utilized for scheduling corrective work.
Predictive Analytics
Dingo’s award-winning Trakka system uses AI and machine learning to predict equipment and process failures with a high degree of confidence. This predictive analytics software solution empowers clients to proactively perform maintenance and minimize cost and downtime while optimizing the lifespan of critical assets.
Dingo’s team of experts analyze customers’ historical failure and monitoring data before making predictions. This allows them to modify or create new machine learning models that will accurately identify any problem areas with equipment. The process involves data collecting, cleansing, and validation. This ensures that models are as accurate as possible. The code-free platform is also easy to use, meaning that anyone can gain valuable, actionable insights from the data.
Helping Maintenance Technicians Make Better Decisions
Dingo’s predictive analytics and condition intelligence systems help technicians make better decisions for maintenance. With access to global benchmarking reports, a troubleshooting guide library, personalized KPI development support, a database of 6 million real-world observations, bi-weekly condition maintenance meetings, and more, Dingo’s solutions provide actionable condition intelligence.
Providing Predictive Maintenance in Mining.
Dingo has provided real-world solutions for the mining industry that meet its daily operational needs and challenges.
A leading global mining company used Dingo’s asset wellness program to save $55 million, helping the mine operator run at the lowest cost per hour. The company operates a huge fleet of 150 haul trucks, 30 loaders, many drills, and 100 underground assets worldwide in its mines. Asset performance was optimized using Dingo’s Trakka® software solutions.
Dingo’s software was applied to a mining excavator swing drive component at the end of its budgeted life. Predictive maintenance allowed the operator to keep the component in healthy condition for an extra 4,000 hours of operation, saving the cost of replacing it.
Mining experts worldwide are utilizing Dingo’s condition-based maintenance programs and cloud computing and storage capabilities to save significant costs and improve the daily operations of critical mining ventures.
Future Opportunities of Predictive Maintenance
Future opportunities exist for predictive maintenance analytics software. The challenges faced by the mining industry in the 21st century will facilitate smarter, more proactive site and operational management systems as the need for cost savings, worker safety, and sustainability become more intensified. Dingo’s asset management expertise places them in a good position to help the mining industry meet these challenges.
References and Further Reading
Iberdrola (2021) Predictive Maintenance: the key data-driven technique for anticipating errors [Online] iberdrola.com. Available at: https://www.iberdrola.com/innovation/predictive-maintenance
Dingo Homepage [Online] dingo.com. Available at: https://www.dingo.com/
Dingo.com (2021) Mining Case Study [Online] dingo.com. Available at: https://www.dingo.com/customer-stories/mining-case-study/
Disclaimer: The views expressed here are those of the author expressed in their private capacity and do not necessarily represent the views of AZoM.com Limited T/A AZoNetwork the owner and operator of this website. This disclaimer forms part of the Terms and conditions of use of this website.