The mining industry produces billions of tons of waste annually and stores it in slag heaps and tailings ponds (Carmo et al. 2020). The mining waste produced contains varying amounts of the target minerals. The point at which mining waste is viewed as ore is determined by people based on financial and environmental factors, such as the cost of extraction or amount of energy it would require using current technology (Lèbre et al. 2017).
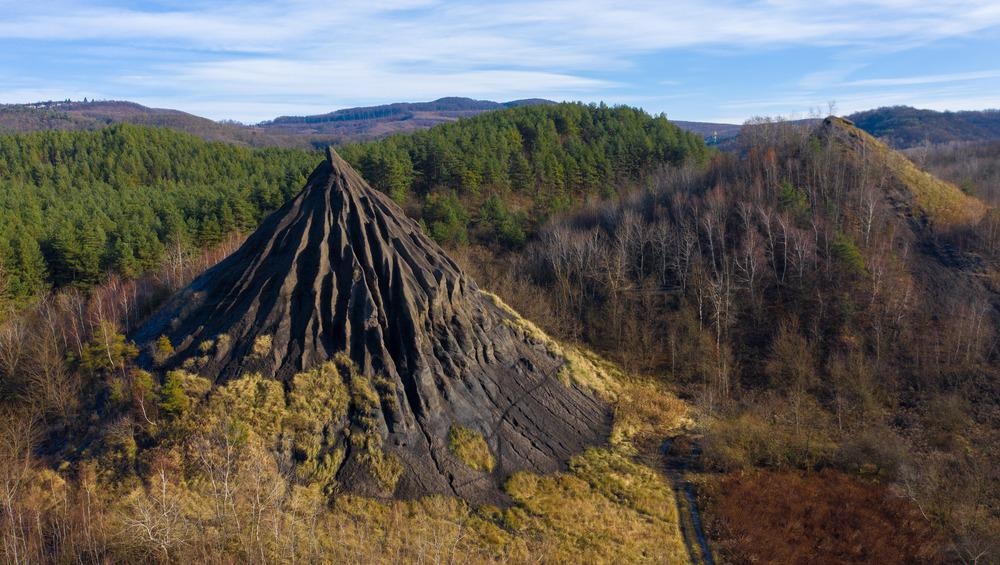
Slag heap left after mining in Salgótarján, Zagyvaróna, Hungary. Image Credit: Airpixel - Drone imagery/Shutterstock.com
As finite mineral resources dwindle and the need for ore waste recycling increases, new methods are being developed to increase the mineral yield of this process.
Slag Utilization Methods
Slag is the waste material produced in pyrometallurgical ore extraction processes such as smelting (Parbhakar-Fox et al. 2019). Depending on the properties of the mineral source rocks, the waste material produced from mines can be used as construction materials, both in infrastructure and in the remediation of the land damaged by the mining (Bian et al. 2012).
The utilization of waste slag in different industries has been gaining momentum since the 1990s (Parbhakar-Fox et al. 2019), meaning that the material can be viewed as a source as well as waste.
Steel slag recycling is a well-implemented method in which, because of the source’s properties, the main byproduct of steel construction can be re-used as a raw material in steel plants or for construction materials in engineering projects.
In many parts of the world such as Japan, the US, and Europe, the utilization rate of steel slag is more than 80% (Guo et al. 2018). This plays an important role in reducing the number of steel reserves used in manufacturing processes.
Steel slag can be utilized in a range of industries, not just for construction materials. Due to its chemical makeup, including two important nutrients for plant growth, phosphorus, and sulfur, steel slag was used to produce fertilizers in Europe in 1880 (Guo et al. 2018). Steel slag also contains magnesium and calcium oxides, so can be used in carbon sequestration processes (Ma et al. 2011, Guo et al. 2018).
Slag Reprocessing Methods
Mining slag can also be reprocessed to recover low-grade ores using hydrometallurgy techniques. A study used sulfuric acid to cause the leaching and concentration of zinc and iron from the waste material in an old lead and zinc mine in Turkey. The study achieved extraction rates of 87% zinc under high pressure and at temperatures of 95 ˚C (Parbhakar-Fox et al. 2019).
Hydrometallurgy techniques such as acidic leaching may become more viable as metal resources decrease and prices increase, but they can be energy-intensive and produce hazardous by-products.
Biometallurgy in Slag Reprocessing
Biometallurgey uses microorganisms to extract target metals from minerals and ores through leaching. These low-cost techniques are used to reprocess slag under normal temperature and pressure conditions. Bioleaching may be less time-efficient than conventional leaching processes, but they require less energy and do not produce hazardous chemicals (Sajjad et al. 2019).
Biometallurgey has been implemented commercially since the 1950s and has become globally utilized because of its low-energy cost and viability on low-grade ores (Sajjad et al. 2019).
Slag heaps contain concentrations of valuable metals that can be dissolved by the acids produced by certain microbes. Copper extraction rates of 91% have been achieved in this way under aerobic conditions (Sajjad et al. 2019).
Tailings Recycling Methods
Porphyry copper deposits are commercially viable if they have a grade of 0.4% (Park et al. 2019). This ore grade would result in 99.6% of the source material going to waste as slag and tailings.
Tailings ponds contain minerals that react in aerobic and aqueous conditions, such as iron and arsenic-baring sulfide minerals, to produce acid that leaches into the environment to cause acid mine drainage.
Tailings recycling methods reduce the volume of these waste products, decreasing the amount of acidic mine drainage and environmental harm. Both kimberlite tailings and steel tailings can be used to construct roads and pavements (Swami et al. 2007, Oluwasola et al. 2015), successfully replacing conventional materials.
Studies even suggest that the use of copper mine tailings in asphalt production could drastically improve its performance. Tailings have also been used in cement and mortar mixtures and have been found to increase their resistance to abrasion (Park et al. 2019).
Implications for The Future
In Japan, the utilization of slag waste is as high as 98.4% (Guo et al. 2018); this may be the most efficient way to combat mining waste issues.
A combination of waste utilization and reprocessing to achieve the maximum extraction rates could be the most appropriate response to tackle mining waste. Environmentally sound, commercially viable methods of reprocessing slag, such as those in biometallurgey, could reduce mining waste and sustainably meet the demand for valuable metals.
Utilizing mining waste in construction materials also replaces conventional building materials, reducing the need for mining in other areas; this is especially relevant in developing areas, which increasingly need building materials to expand infrastructure.
References and Further Reading
Bian, Z., Miao, X., Lei, S., Chen, S.E., Wang, W. and Struthers, S., 2012. The challenges of reusing mining and mineral-processing wastes. Science, 337(6095), pp.702-703. https://www.science.org/doi/abs/10.1126/science.1224757
Carmo, F.F., Lanchotti, A.O. and Kamino, L.H., 2020. Mining Waste Challenges: Environmental Risks of Gigatons of Mud, Dust and Sediment in Megadiverse Regions in Brazil. Sustainability, 12(20), p.8466. https://www.mdpi.com/2071-1050/12/20/8466
Guo, J., Bao, Y. and Wang, M., 2018. Steel slag in China: Treatment, recycling, and management. Waste management, 78, pp.318-330. https://www.sciencedirect.com/science/article/pii/S0956053X18302691
Lèbre, É., Corder, G.D. and Golev, A., 2017. Sustainable practices in the management of mining waste: A focus on the mineral resource. Minerals Engineering, 107, pp.34-42. https://www.sciencedirect.com/science/article/pii/S0892687516304071
Ma, G.J., Tang, H. and Jin, Y.B., 2011. Mineral sequestration of CO2 using basic oxygen furnace (BOF) steelmaking slag. In Advanced Materials Research (Vol. 194, pp. 2140-2144). Trans Tech Publications Ltd. https://www.scientific.net/AMR.194-196.2140
Parbhakar-Fox, A., Gilmour, S., Fox, N. and Olin, P., 2019. Geometallurgical characterization of non-ferrous historical slag in western Tasmania: identifying reprocessing options. Minerals, 9(7), p.415. https://www.mdpi.com/2075-163X/9/7/415
Park, I., Tabelin, C.B., Jeon, S., Li, X., Seno, K., Ito, M. and Hiroyoshi, N., 2019. A review of recent strategies for acid mine drainage prevention and mine tailings recycling. Chemosphere, 219, pp.588-606. https://www.sciencedirect.com/science/article/pii/S0045653518321568
Sajjad, W., Zheng, G., Din, G., Ma, X., Rafiq, M. and Xu, W., 2019. Metals extraction from sulfide ores with microorganisms: The bioleaching technology and recent developments. Transactions of the Indian Institute of Metals, 72(3), pp.559-579. https://link.springer.com/article/10.1007/s12666-018-1516-4
Disclaimer: The views expressed here are those of the author expressed in their private capacity and do not necessarily represent the views of AZoM.com Limited T/A AZoNetwork the owner and operator of this website. This disclaimer forms part of the Terms and conditions of use of this website.