One of the biggest obstacles to rescuing miners after an accident is the unknown level of danger, which can derail rescue operations and even put rescuers' lives in danger. In such circumstances, the contribution of mobile underground robots becomes crucial.
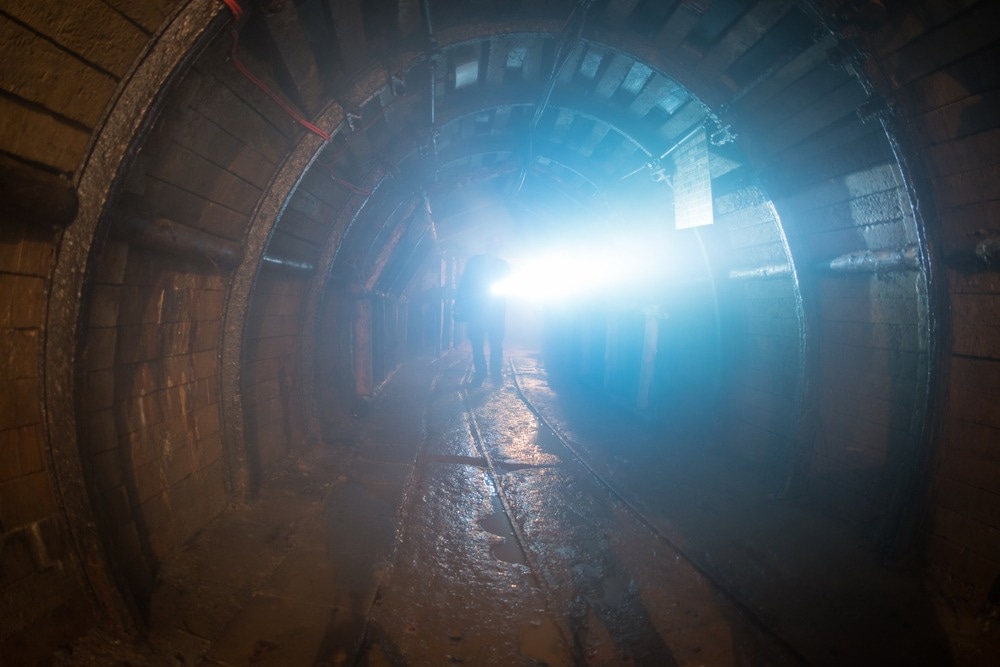
Image Credit: Przemek Tokar/Shutterstock.com
Why are Robots Needed in Underground Mines?
When an incident occurs in a mine, it is crucial to contact the victims as quickly as possible. In addition to a lack of oxygen, the accident zone contains elevated amounts of hazardous gases such as carbon monoxide and carbon dioxide, as well as explosive gases such as methane.
The mine is filled with dust and smoke, obstructing the visibility of the rescue team. Such potentially lethal circumstances present several obstacles for the rescue teams and hamper their ability to assess the situation swiftly and effectively.
Robots can provide crucial information safely to teams engaged in search and rescue operations.
Advantages of Using Robots in Mining Rescue Applications
Regardless of the condition of the mine, the robot can be put to use immediately after an accident. A mine rescue robot can provide sufficient supplies, including oxygen cylinders and medicine. The robots are equipped with various sensors that alert trapped miners of possible gas leakage.
Based on the data provided by the robot, the rescue command center can devise an effective rescue strategy. These robots can also assist in mapping and data collection of difficult-to-reach places in a mine.
Functions of Robots in Mining Rescue Operations
Searching
The rescue robots conduct precise and controlled search operations in the unstructured and dark mines to detect potential dangers or locate victims. These search activities must be completed rapidly without risking victims or rescuers.
Mapping and inspection
The robots update the rescue crew with information about the surroundings and quickly create a map of the demolished region. The rescue robot can calibrate its path with the help of vision sensors installed on the industrial robots operating inside the mine.
Structural examination
The sensors allow the robot to determine the most efficient route through obstacles to expedite safe and secure rescue operations. Surveillance of the mine using onboard live video transmission and lighting enables the rescue crews to prepare accordingly. Robots with thermal cameras can locate the victims quickly with the help of their body temperature.
Rescue robots can also move debris that would otherwise block mining rescue operations. The robots have a variety of temperature and gas sensors for constant surveillance of the surrounding environment, allowing rescuers to make faster and more intelligent decisions.
Research and Development
Gemini Scout
Sandia Laboratories have designed the Gemini-Scout robot for mining rescue operations, which detects the dangers that may threaten the rescue team and can provide some direct basic help to the trapped miners.
The robot climbs rocks and rubble piles to assess the degree of risk of each section of the mines and help find the best path to reach the miners.
The robot uses gas sensors, a thermal camera to find survivors, and another camera mounted higher to see the obstacles it approaches.
Groundhog
The Groundhog rescue robot was created by Carnegie Mellon University (CMU) for autonomous mapping and exploration of abandoned underground mines. Groundhog has been used in the surveillance of many abandoned coal mines and completed nine autonomous missions during its lifetime. By capturing a significant range of data and video, it was able to create high-quality maps and models of the mines.
Wolverine V2
The Wolverine was purchased from Remotec by the Mine Health and Safety Administration (MHSA). It was a military robot, but it was modified for mining rescue operations.
It has gas sensors for uninterrupted sampling and cameras controlled remotely through a fiber-optic tether. It is intended for use from a secure distance of 5000 feet and delivers vital data and a live video feed of the mining rescue operations.
Australian Droid & Robot
Australian Droid & Robot (ADR) employed robots to reach 1.7 km into a limestone mine in the Southern United States. After the mine collapsed, robots scanned and inspected the mine's geometry. Wireless networking was made with Rajant Kinetic Mesh to establish real-time low latency and long-distance networks.
The deployed robots had a universal platform that contained gas sensors, LIDAR (Light Detection and Ranging) systems, robotic arms, and high-quality pan tilt zoom cameras.
The Future of Robots in Mining Rescue Operations
Artificial intelligence and robotics have propelled us into a new era of automation. The rescue robots will make post-disaster mining rescue operations safer than ever.
They can assist in surveillance of the accident site, locate the survivors and deliver first aid to them, and update the rescue crew about the mine's environmental conditions.
Several rescue robots are currently being developed, and a few have been tested in real-world circumstances, albeit with unsatisfactory outcomes. The challenge for the industry is to make more advanced, smarter rescue robots with strong and reliable hardware to work in dangerous zones and handle any problems that might arise.
Numerous lives have been saved by the use of rescue robots in various industries worldwide. If this technology is employed in mines, this number might increase exponentially.
References and Further Reading
CDC. (2017). Mining Feature: MSHA Media Event Highlights Mine Rescue Capabilities. [Online] Centers for Disease Control and Prevention. Available at: https://www.cdc.gov/niosh/mining/features/mshahighlightsminerescue.html (Accessed on 10 June 2022).
Hardy, E. (2022). The Challenges of Completing the World's Deepest Remote Underground Mine Inspection. [Online]. Create Digital by Engineers Australia at: https://createdigital.org.au/deepest-remote-underground-mine-inspection-in-history/ (Accessed on 10 June 2022).
Reddy, A. H., Kalyan, B., & Murthy, C. S. (2015). Mine rescue robot system–a review. Procedia Earth and Planetary Science, 11, 457-462. https://doi.org/10.1016/j.proeps.2015.06.045
Zhai, G., Zhang, W., Hu, W., & Ji, Z. (2020). Coal mine rescue robots based on binocular vision: A review of the state of the art. IEEE Access, 8, 130561-130575. https://doi.org/10.1109/ACCESS.2020.3009387
Disclaimer: The views expressed here are those of the author expressed in their private capacity and do not necessarily represent the views of AZoM.com Limited T/A AZoNetwork the owner and operator of this website. This disclaimer forms part of the Terms and conditions of use of this website.