Many challenges face the mining industry in the 21st century. This article will discuss how mechanized development technology is being used to solve these challenges, and what the future holds for the field.
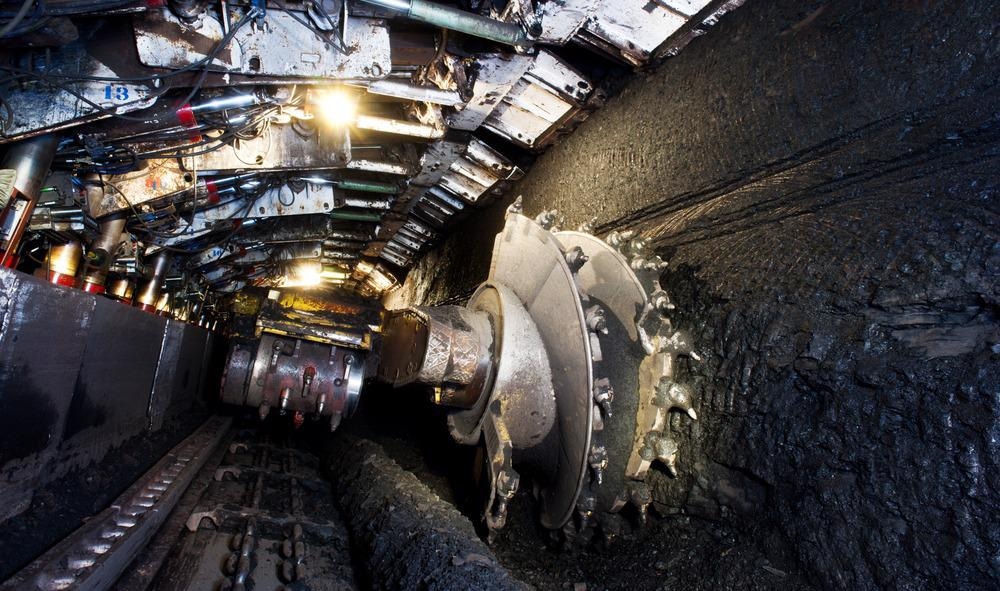
Image Credit: Wirestock Creators/Shutterstock.com
What is Mechanized Development Technology in Mining?
For centuries, mining was carried out by hand and with animals until the advent of industrialization. Over the past couple of centuries, ever more sophisticated equipment has been developed to exploit resources more efficiently and safely.
Mechanization is increasingly being utilized by many industries including the mining industry. Mines have increasingly employed mechanized machinery such as hydraulic props and beams (replacing wooden beams) as well as numerous other improvements in mining technology. This has many advantages for modern mining over traditional processes.
What is the Importance of Mechanized Solutions in Mining?
Numerous challenges exist in the mining industry that mechanization is being used to solve. Mechanized development technology makes mines safer, can find and exploit resources more efficiently, and helps to design better mines.
Mechanized development technology is currently being developed in numerous ways worldwide. For example, since 2000, China has been improving its FMM technology while updating safety mechanisms in its mines. For example, thin seams (which have a thickness of less than 1.3 m) occur in more than 80% of all Chinese coal mines. Thin seam coal mining presents technical challenges including substandard working conditions, complex field management, confined spaces, and high labor intensity.
Implementing fully mechanized mining solutions, therefore, improves the safety of thin-seam mining, while also improving the overall resource extraction and economic viability of mines. Numerous other mining companies worldwide are currently implementing mechanized solutions to their historical woes in extracting resources.
Recent Developments in Mechanized Technology for Mining
In China in 2014, fully mechanized mining (FMM) face output reached 10 million tons (Mt) of coal, out of a total of 3465 Mt. China is the biggest producer of coal, being responsible for over 50% of total global output in 2020. As explained before, thin-seam coal mining is present in around 85% of all Chinese mines and the extraction of this resource in this environment is problematic.
Between 2006 and 2010, the MG100/238-WD drum shearer was used successfully in Chinese mines to exploit thin seams. This fully mechanized equipment, which is conveyor-mounted, can cut seams of coal 0.8-1.25 m thick. This technology broke through the 1.0 m limitation of Chinese FMM technology, significantly increasing thin seam exploitation potential. Other developments have demonstrated that thin seams of 1 m thickness can yield 1 Mt per year if the right equipment is used.
Other FMM technologies in China have been implemented for seams of ultra-large thickness, and fully mechanized top coal caving technology has also been implemented in many mines. This method was developed in Europe, but not commonly implemented globally. Fully automated backfilling technology has also been developed in recent years.
Vietnam, while a smaller producer (48.4 Mt output in 2020), has also been developing FMM technologies in its mines.
From 2002-2005, Khe Cham Coal Mine in Vietnam exploited 512,918 tons of coal, with the highest monthly output reaching 22,300 tons, with an average of 5.16 tons per man-shift. Technologies employed were the longwall mining method, with coalfaces supported by self-moving hydraulic beams, and automatic shearers were used to exploit the full thickness of the seam.
In 2005, based on the results of the trial period, the Khe Cham Coal Mine implemented the first fully mechanized mining technology in Vietnam.
Vang Danh coal company implemented fully mechanized mining technology in 2007, rapidly increased coal production from thick seams, dipping to 35o using mechanized coal shearers, armored face conveyors, and self-acting shield support equipment.
Between 2015 and now, VINACOMIN (the Vietnam National Coal and Mineral Industries Group) has implemented new LTCC (longwall top coal caving) technology in three of its underground mines. Ha Lam Coal Mine alone has had the capacity for 1,200,000 tons per year since 2016.
The Indian mining industry is fast heading towards a technology-driven mining ecosphere. Improvements in AI, machine learning, and the internet of things has improved the automation of machinery operation and planning. It has also improved predictive maintenance, real-time data, and analytics usage, and provides vastly improved traceability of assets and materials. One specific use of AI is to provide real-time monitoring of excavator shovel teeth conditions and continuous estimation of rock size in the shovel bucket.
How are Recent Developments Improving Mining Applications?
Mechanized applications help to improve mining applications in many ways. Asset management, traceability, safety, intelligent mine design and improved resource extraction, and economic viability of mines are all being positively impacted by this technological revolution.
Mechanized development technology has provided distinct advantages over traditional labor-intensive methods of mining. In Vietnam, for example, data from recent tests and commercial operations have shown that mining and labor cost is lowered, and labor productivity is increased. Because the main task in mining, the breaking apart and extraction of the resources, is fully mechanized at the face, worker safety and conditions are significantly improved and fewer workers are needed at the face.
AI-based solutions in India are making fully automated mining operations that are dynamic and can predict problems before they arise possible. While problems persist in implementing FMM technology widely, full mechanization of mining operations is the ultimate prize for the industry in the 21st century.
What is the Future of Mechanized Development?
Recent developments continue to drive the mining industry forward into the 20th century and beyond. Technical problems such as the application of FMM equipment to complex seams still presents issues, demonstrating that the field has some way to go before full mechanization of mining operations is possible.
However, the development of fully mechanized mining equipment and complementary technologies such as AI and machine-learning is exciting for the industry, and the future underground is set to become progressively more automated.
References and Further Reading
Duc, H.D. et al. (2021) Development orientation of mechanized technology of underground mining in Quangninh coalfield, Vietnam AIP Conference Proceedings 2209, 020004 [Accessed online 7th October 2021] https://aip.scitation.org/doi/pdf/10.1063/5.0000005
Wang, J. (2014) Development and prospect of fully mechanized mining in Chinese coal mines International Journal of Coal Science & Technology 1, pp. 253-260 [Accessed online 7th October 2021] https://link.springer.com/article/10.1007/s40789-014-0017-2
Indian Infrastructure (2021) Trending Technologies – Creating a digitally enabled environment in mining [Accessed online 7th October 2021] https://indianinfrastructure.com/2021/03/18/trending-technologies/
Disclaimer: The views expressed here are those of the author expressed in their private capacity and do not necessarily represent the views of AZoM.com Limited T/A AZoNetwork the owner and operator of this website. This disclaimer forms part of the Terms and conditions of use of this website.