The mining industry utilizes various specialized components for different purposes. For the purpose of water recycling, thickeners play an essential role in the mining industry. Apart from their efficiency, the cost-effectiveness of the process and this component makes it a viable option.
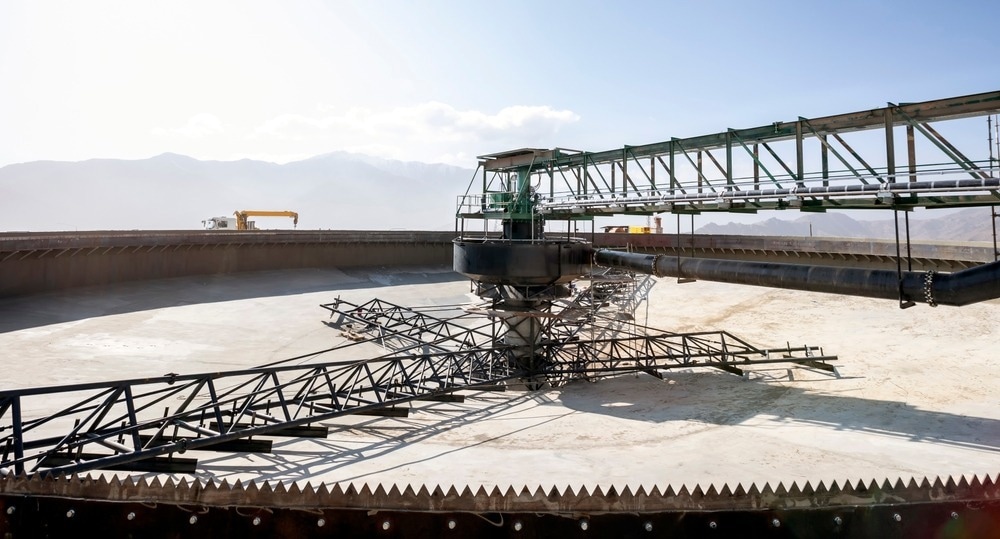
Image Credit: Funtay/Shutterstock.com
What is the Process of Thickening in the Mining Industry?
Thickening or dewatering is the elimination of a component of the liquid from a pulp or slime composed of intricately separated solids and liquids. It is described as persistent dehydration of a diluted pulp in which a periodic outflow of uniformly dense viscous pulp occurs simultaneously with an overflow of cleared solution. A thickener is a device that filters liquids from solids. Thickeners were first used in the mining business in 1905.
Why Thickeners are Important for the Mining Business?
Thickeners are commonly used in hydrometallurgical operations to produce concentrate from raw ore and to enhance the solid content of the concentrate mixture (concentrate + treatment water) so that the highly-dense slurry can be supplied successfully and the recycling of process water can take place efficiently. The gravel and mining sectors, as well as ecological professionals, employ high-rate thickeners to recover roughly 85 percent of water for reuse.
Which Factors Affect the Performance of a Thickener?
Key factors for successful thickener control include bed level, bed mass inventory, underflow density, overflow transparency, and flocculent dosage. All these factors and measures are difficult to determine, and precision and dependability must be considered while selecting and installing the appropriate equipment.
Applications of Thickeners in the Mining Sector
As mentioned above, dewatering operations utilize it substantially. The utilization of a high-efficiency thickener for red ore integrated by centrifugation can achieve greater underflow concentrations and raise the dehydration velocity of the concentrate. Furthermore, the adoption of an angled sheet design high-efficiency thickener improves dehydration. The use of inclined plate thickening alters the deposition route of mineral grains, minimizes the consumption of coagulant, and significantly enhances the thickener's dehydration performance.
Working on a Thickener
It operates on the gravity sedimentation method, and the most typical thickening structure is iron or steel. A cylindrical tank houses the continuous thickener. Pulp is supplied into the tank's midsection via a feed-well located up to 1 m underneath the suspension's exterior.
Scraper edges or rollers, powered by an effective framework, rotate slowly over the tank's bottom, which normally curves moderately toward the center, to transport debris accumulated on the bottom to a centralized aperture or outlet. The rakes circle at a rapid enough velocity to transfer the sediment as quickly as it settles without causing too much disturbance.
Do Flocculants Improve the Performance of Thickeners?
Flocculant is one method for increasing the effectiveness of thickeners. The high-efficiency thickener incorporates flocculants into the pulp as it enters the thickening, considerably improving the operational parameters of conventional thickeners.
Anionic and non-ionic flocculants are commonly used in concentrators. Because of the ore's variable surface electrical characteristics, the relevant flocculant models vary, and the decision of the specific model flocculant must be validated by experiments. Before concentrating, the best flocculants can be selected based on the qualities of the concentrated pulp.
Types of Thickeners
Thickeners are split into two categories based on the placement of the rake driving mechanism. They are classified as either centrally or laterally operated. Furthermore, there are two types of centrally driven varieties based on the way of holding the operational mechanism and the raking arms. These are the column type and bridge type thickeners.
The column type thickener is the one in which central steel or concrete pillar takes the reaction to the load of the device in the vertical direction and the twisting stress horizontally. A framework bridges the reservoir of the bridge type and is forced vertically to the mass of the device, plus any sediments that build inside the arms truss, as well as laterally to the twin forces exerted by the gravity of the sloped underflow.
Various manufacturers created machines described as "high capacity" or "high rate" thickeners in the 1980s. These machines differ from traditional installations in that they require less unit space.
Latest Research
The latest article by Wu et al. in the International Journal of Minerals, Metallurgy and Materials is concerned with the smooth and effective functioning of paste thickeners which is heavily reliant on the optimal design of integrated components. When underflow discharge is halted, the flow unit is primarily responsible for reducing the enormous torque that the residual particles within the thickeners may put on rakes.
To represent the variations in underflow high viscosity content and yield stress, a numerical theoretical model was established. The major characteristics of the circulatory device, namely the elevation and flow rate, were adjusted in the trials to assess its performance.
The results suggested that the circulatory device is effective at lowering underflow granular percentage and yielding stress to an acceptable degree, and the concept may be used to explain its effectiveness at different elevations and discharge rates. A good circulatory unit development and selection adds to the cost-effective functioning of paste thickeners.
To summarize, thickeners play an essential role in various industries so companies such as Westech, and Dorr-Oliver are investing heavily in their research and development. Further studies revolving around effective weight and area reductions would certainly help in increasing its effectiveness manyfold.
References and Further Reading
Li, H. et al. (2021). Changes in underflow solid fraction and yield stress in paste thickeners by circulation. International Journal of Minerals, Metallurgy and Materials, 28(3), 349-357. Available at: https://doi.org/10.1007/s12613-020-2184-z
LongZhong Machinery, 2022. The Application of Thickener in Mining Industry. [Online] Available at: https://www.lzzgchina.com/solutions/project-case/the-application-of-thickener-in-mining-industry.html [Accessed on 16 May 2022].
Murphy, E., 2022. Thickener upgrade: where financial and sustainability overlap. [Online] Available at: https://www.australianmining.com.au/ [Accessed on 16 May 2022].
Savona Equipment, 2018. Thickeners — Types, Working Principle & Applications. [Online] Available at: https://medium.com/@marianna_56839/thickeners-types-working-principle-applications-3d92a3725e8a [Accessed on 16 May 2022].
Hosseini, N. M. (2014). The application of zeolite in thickeners for optimal water recovery and preventing environmental pollution. Recycling and Sustainable Development, 7(1), 30-34. Available at: https://doi.org/10.5937/ror1401030H
Disclaimer: The views expressed here are those of the author expressed in their private capacity and do not necessarily represent the views of AZoM.com Limited T/A AZoNetwork the owner and operator of this website. This disclaimer forms part of the Terms and conditions of use of this website.